Wet Sugar Bucket Elevator for Amalgamated Sugar
Amalgamated Sugar
Twin Falls, ID
General Description
The United States is among the world’s largest sugar producers. Sugar is produced from both sugarcane and sugarbeets. Sugarcane accounts for approximately 45-percent of the total sugar produced domestically, and sugarbeets account for approximately 55-percent of production. US sugar production continues to expand with additional investment in new technologies, processes, and equipment.
Amalgamated Sugar is the second largest manufacturer of sugar from sugarbeet in the US and sells sugar across the country through National Sugar Marketing Cooperative. Growers raise sugarbeet on approximately 180,000 acres of prime irrigated land, producing 7,000,000 tons of sugarbeet annually. Operating 24/7, sugarbeet is processed during the fall and winter, producing sugar 11 months per year, and molasses separators are operated year-round. Amalgamated Sugar works closely with growers to improve sugarbeet crops produced through research, striving for data driven excellence.
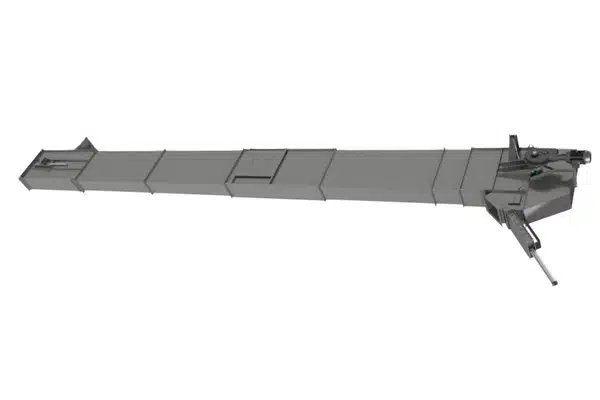
KWS Bucket Elevator Delivers 50-Percent More Capacity
Design Parameters
- Product Type: Wet Sugar
- Material Density: 55 to 63 Lbs. per Cubic Foot
- Capacity: 2,500 Cubic Feet per Hour
- Duty: 24/7
KWS Advantages
KWS and Amalgamated Sugar have had a long-standing relationship and together have solved many bulk material handling problems. Engineers from KWS made several site visits and took field measurements of an existing bucket elevator. 3D models of the specific area of the plant were created to eliminate any interference and to work around space constraints. KWS has the experience of designing equipment to perfectly suit an application without the need of a third-party engineering firm or detailed specifications. The project needed to be designed and built on a quick timeline and KWS was up to the challenge. KWS supplied the equipment 2 months early and satisfied the customer’s quick lead time requirements.
KWS Special Features
The new bucket elevator was designed to fit the exact same footprint as the existing unit but with an increased capacity of 50-percent. Bucket size and spacing was carefully considered in the new design. The new unit was constructed from 304 stainless steel for longevity and corrosion-resistance.
KWS provided a special spring-loaded telescoping take-up on the boot section to automatically compensate for chain stretch and wear. The telescoping take-up maintains chain tension under varying thermal conditions and absorbs bucket-to-wall hangups in the bucket elevator to minimize the occurrence of the chain jumping the sprocket during operation. The take-up also uses standard pillow block bearings for easy maintenance so bearings can be changed out in minutes.
KWS provided a direct-drive shaft mounted reducer with fewer components in the drive assembly to reduce the footprint when compared to a belt driven arrangement. There are no belts to replace or noisy chains to maintain and lubricate making the shaft mount design easier for maintenance.
A special pneumatic slide gate was located on the bucket elevator discharge to isolate downstream equipment as required. The unique design saved space and connected directly to a transfer screw conveyor without the need for an intermediate connection between the two.
Testimonial
"I appreciate the great work KWS has put into this design with excellent communication. It has been a positive experience working with KWS through this purchase."
Chad Larsen, Project Manager – Amalgamated Sugar
Slide Gate is Integrated with Bucket Elevator Discharge
Direct Drive Reducer Saves Space and Reduces Components
Spring-Loaded Telescoping Take-Up Keeps Constant Tension on Chain