Screw Feeder for Pyrolysis Reactor
General Description
As more industrial processes transition to renewable energy sources, companies are finding new ways to power equipment such as boilers, air heaters, and chillers which typically rely on the combustion of fuels such as natural gas and coal. Developing bioenergy solutions that are more efficient, flexible, and environmentally friendly is important for reducing greenhouse effects and our overall carbon footprint. Biomass in the form of wood chips is a renewable resource. Pyrolysis is the thermal degradation of wood chips that occurs in the absence of oxygen. The resulting products are oil, biochar, and gas. Pyrolysis oil can be gasified to syngas and further converted to biofuel. KWS designed and provided a special high temperature screw feeder to meter wood chips into a pyrolysis reactor.
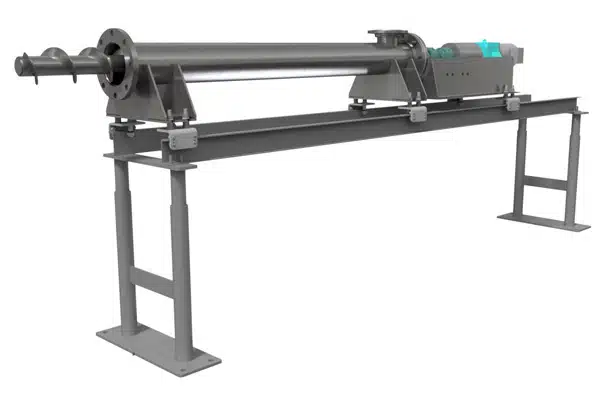
Cantilevered Screw Feeder Meters Woods Chips into Pyrolysis Reactor
Design Parameters
- Product Type: Wood Chips
- Design Temperature: 1,300 to 1,800-degrees F
- Design Pressure: 5-psig
- Material Density: 13 to 20 Lbs. per Cubic Foot
- Capacity: 24 Cubic Feet per Hour
- Duty: Intermittent
KWS Advantages
KWS has extensive experience conveying bulk materials at high temperature and an understanding of the pyrolysis process. Knowledge of metallurgy and high temperature stainless steels were also important for solving this difficult problem.
Screw Extends into Reactor and Operates at 1,800-Degrees F
KWS Special Features
KWS designed and manufactured the screw feeder from 310 stainless steel to handle the high temperature inside the reactor. The outer housing was seamless pipe with 150-Lb. ANSI flange connections to ensure the unit would hold pressure. Extreme heat gasket material was used on the ANSI flange connections. Since the screw injected wood chips into the reactor at 1,800-degrees F, KWS designed the screw feeder as a cantilever. A cantilever screw is only supported on the inlet end by the drive shaft and two bearings. The cantilevered design allows bulk materials to discharge directly from the end of the conveyor and eliminates the need for a tail bearing in the breach of the reactor. The double bearing arrangement on the inlet end is designed to handle the cantilevered load of the screw as well as thrust loads and misalignment. The drive pedestal was designed to protect the gear reducer and motor from heat. The gear reducer and motor are located away from the heat source and operate at ambient temperature. The pedestal design also provides easy access to the shaft seal, gear reducer, motor, low-speed coupling, and bearings for maintenance.
The cantilevered screw feeder was mounted on a rail system that consisted of adjustable vertical supports and equipped with feet and rollers to allow the unit to be moved axially for safe access to the reactor.
Testimonial
"It has been a great experience working with KWS. We are looking forward to working with you on the full-scale product facility in the future."
Project Engineer – Pyrolysis Engineering Company
Drive Pedestal Protects Gear Reducer, Bearings, and Motor from Heat
Rail System is Equipped with Rollers to Allow the Screw Feeder to Move Axially