Screw Conveyor with Low Profile Slide Gates
General Description
Many modern cigars are made of three components: a wrapper, binder, and filler. In an effort to keep up with demand at a reasonable price point, machines are extensively used in the process as opposed to hand-rolled alternatives. At a tobacco facility in CT, bulk tobacco is brought in, sorted, and conveyed through various processes via screw conveyors. Enclosed screw conveyors contain potentially flammable tobacco dust, thereby decreasing cleanup costs and eliminating a potential risk to the process.
One particular step in the cigar making process requires tobacco materials to be fed into a single line from nine different sources to achieve a particular product mix. Each hopper contains a certain type of tobacco and loading is automated via pneumatically controlled slide gates. Due to space constraints, a standard slide gate would not fit between the hopper flange and screw conveyor inlet. Knowing this, KWS designed and provided nine low profile slide gates to fit in the limited vertical space while retaining the benefits of the standard KWS solution.
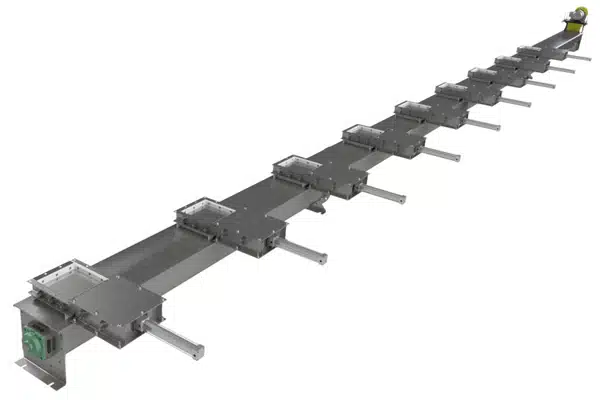
KWS Provided 9 New Low-Profile Slide Gates Above Existing Screw Conveyor
Design Parameters
- Product Type: Tobacco Stems & Leaves
- Material Density: 19 Lbs. per Cubic Foot
- Capacity: 947 Cubic Feet per Hour
- Duty: 24 Hours per Day, 7 Days per Week
KWS Advantages
Designing a custom solution required a balance between meeting the capacity requirements of the plant and providing equipment that would fit within the dimensional constraints without costly modification. Based on capacity requirements and space constraints, slide gate sizing was determined. Field measurements were collected and KWS determined that a low-profile slide gate was required. With over 50 years of experience in providing solutions in the bulk material handling market, KWS created a custom, low profile design based on the KWS standard roller slide gate that fit and worked perfectly for the application.
KWS Special Features
KWS flat pneumatic slide gates utilize bronze bushed rollers to support the slide plate in lieu of key stock, which reduces friction and allows for easy actuation. UHMW wipers surround the inside perimeter of the gate opening to provide 100-percent discharge and prevent material from being pulled into the gate housing. As a result, the gate will easily remain fully open or fully closed as required for the application. A three dimensional model was developed to determine the minimum clearance required for the rollers to function correctly, resulting in the modified gate frame needed to fit in the customer’s space.
Testimonial
"The KWS slide gate design allowed us to automate the process through a PLC, which was critical for us. KWS kept us from having to allocate an employee to operating hand slides full time and saved us a ton of money."
Plant Maintenance Manager
Each Slide Gate Introduced Specific Tobacco Ingredients to the Process
Space Constraints Created the Need for a Low-Profile Slide Gate
Slide Plate is Supported by Low-Friction Bronze-Bushed Rollers
UHMW Wipers Surround Perimeter for 100-Percent Discharge