Redesigned Screw Conveyor for Kingsford Charcoal in Belle, MO
General Description
Since 1920, Kingsford Charcoal has been the gold standard for grilling. Kingsford charcoal is made from charred soft and hardwoods such as pine, spruce, hickory, and oak, depending on which regional manufacturing plant it comes from. The char is then mixed with ground coal and other ingredients to make a charcoal briquette. More than one million tons of wood scraps are converted to charcoal briquettes annually.
Raw materials, primarily wood waste from regional sawmills, comprise the ingredients for manufacturing. Wood waste undergoes magnetic filtration to remove any metallic items, then is ground into fine particles and purged with hot air to remove moisture. The wood particles are later charred in a large furnace with multiple hearths in a controlled-oxygen atmosphere. The wood charring process is progressive from one hearth to the next. The charred wood particles are then combined with the other ingredients, press formed into pillow-shaped briquettes and dried before being packaged for sale.
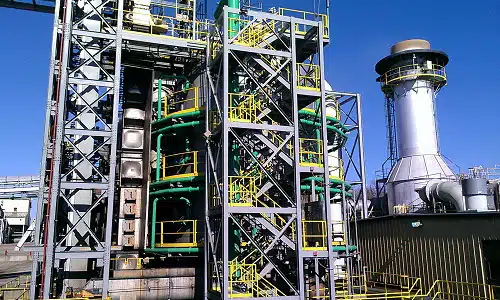
Wood Waste is Converted into Charcoal Briquettes at Kingsford
Design Parameters
- Product Type: Sawdust and Wood Dust
- Material Density: 15 Lbs. per Cubic Foot
- Capacity: 3,500 Cubic Feet per Hour
- Duty: 24 Hours per Day, 7 Days per Week
KWS Advantages
With uncompromised quality and customer service, KWS produces custom-engineered conveyors for the bulk material handling industry. Together, Kingsford and KWS create real-time solutions with a focus on maximum production and zero downtime. The harsh and unrelenting environment in charcoal production requires only the best equipment. The solutions created by Kingsford and KWS are a permanent return on investment that enhances reliability and productivity. KWS also provides field support, troubleshooting and training to achieve solutions that make a difference.
KWS Special Features
KWS field engineers and Kingsford personnel combined to create solutions for an existing screw conveyor that was aging, required constant maintenance, and needed upgrades. The existing screw conveyor had a hanger and bearing that while providing support, also created a wear point that needed to be addressed. KWS designed and manufactured a completely new conveyor using large diameter pipe, reducing deflection at mid-span of the screw, and eliminating the hanger and bearing. The flights and OD of the screw were hardsurfaced with an alloy to resist abrasion and the harsh environment. All welding was performed by AMSE certified welders to ensure only the highest quality.
Components such as the drive shaft were machined in CNC lathes and mills to an accuracy within 0.001-inches. Special four-bolt connections on both ends of the screw with custom machined bolt pads provided ultimate strength at all connections. In process and final inspection was performed by KWS Quality.
Testimonial
"The new redesigned KWS screw conveyor is performing flawlessly. Our inspections show no wear, and it operates just as promised."
Angie Lee, Maintenance Planner – Kingsford
Kingsford Charcoal is the Gold Standard for Grilling
Charred Wood and Other Ingredients Make Up Kingsford Charcoal Briquettes
New KWS Screw Conveyor Eliminates Maintenance Problems
One-Piece Screw Operates Continuously with No Downtime