Metering and Conveying Silica Sand for Sedron Technologies
General Description
Safe drinking water and clean sanitation systems are basic needs for everyone in the world. However, approximately 4.5 billion people do not have access to these necessities. Viruses and diseases spread due to poor sanitation. Traditional sanitation systems are not feasible in certain areas of the world. New technology is needed to solve the problem of poor sanitation. Fortunately, many new ideas and developments are helping to create safe drinking water and clean sanitation.
Sedron Technologies developed a decentralized waste treatment system using a Janicki Omni Processor that kills pathogens while recovering valuable resources from biosolids and other waste streams. The Omni Processor processes waste without piped water, sewer or electrical connections and can transform waste into useful resources such as energy and water. The process starts with biosolids mixed with hydrated lime and silica sand being fed to a dryer where moisture is removed. The dried solid waste is then burned to produce heat in a boiler to generate steam and power a turbine generator to produce electricity. The electricity powers the processor with excess electricity sold back to the power grid.
For more information about Sedron Technologies and the Janicki Omni Processor, watch the Netflix documentary “Inside Bill’s Brain: Decoding Bill Gates” or go to YouTube for various videos on the Janicki Omni Processor.
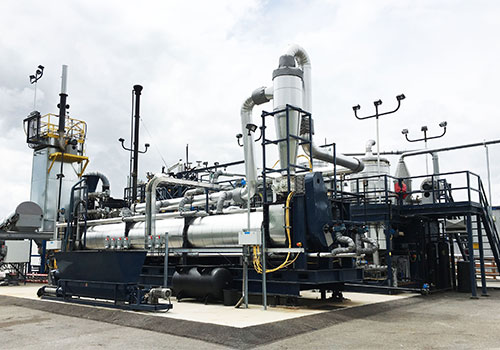
KWS Provides Critical Equipment to Sedron Technologies
Design Parameters
- Product Type: Silica Sand
- Material Density: 92 Lbs. per Cubic Foot
- Conveyor System Capacity: 23 Cubic Feet per Hour
- Duty: 24 hours per Day, 7 Days per Week
KWS Advantages
KWS has been working with Sedron Technologies on several phases of the Janicki Omni Processor waste treatment system and provided bulk material handling equipment for metering biosolids to the boiler to generate electricity. For this phase of the project, Sedron Technologies needed a screw feeder for metering silica sand from a hopper and an inclined screw conveyor to transfer the silica sand into the biosolids for mixing. Using 3D model concepts generated by Sedron Technologies, KWS provided a quick engineered solution that fit seamlessly into their process.
Special Features
The new KWS screw feeder was equipped with an elongated inlet to fit a chisel-bottom mass-flow hopper. Variable pitch screw design evenly draws the silica sand from the hopper and avoids rat-holing to promote first-in-first-out mass flow. Immediately after the inlet, a feeder shroud provides accurate metering and reduces trough loading. A specially designed discharge transition allows smooth flow into the inclined screw conveyor. The inclined screw conveyor elevates the silica sand and discharges to a mixer. Tubular housing design increases conveying efficiency when conveying bulk materials up an incline over 20-degrees.
All screws were constructed from abrasion resistant AR235 material to increase equipment life. Split gland seals keep the silica sand contained within the screw feeder and inclined conveyor.
Testimonial
"We have used KWS for several of parts of the Omni Processor project. Having reliable equipment is a must for our applications which is why we continue to use KWS."
Mathew Bartholow, Engineer – Sedron Technologies
Screw Feeder Meters Sand to Inclined Screw Conveyor
Elongated Inlet of Screw Feeder Fits Chisel-Bottom Mass-Flow Hopper
Tubular Housing Design and Abrasion Resistant Construction Provide High Efficiency and Long Service Life