Metering and Conveying Raw Materials for Making Glass
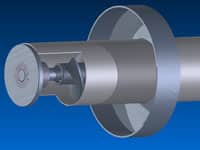
GE Consumer & Industrial
Bridgevill, PA
General Description
GE Consumer & Industrial, a global leader in the lighting industry was in need of metering and conveying equipment for their glass plant in Bridgeville, PA. They needed to meter dry, free flowing raw materials from five different storage bins as part of the glass making process. Some of the raw materials used in making glass are silica, sodium carbonate, calcium oxide, lead and boron. Metering accuracy is very important for producing high quality glass for consumer use. The various raw materials were metered from each storage bin and transferred by screw conveyor to a weigh hopper for addition to their process.
Design Parameters
- Product Type: Various Raw Materials – Silica, Sodium Carbonate, Calcium Oxide, Lead and Boron
- Material Characteristics: Mildly Abrasive and Free-Flowing
- Material Density: 40 to 90 Lbs. per Cubic Foot
- Capacity: 40 Cubic Feet per Hour per Screw Feeder
- Duty: 24 Hours per Day, 7 Days per Week
KWS Advantages
Engineers from KWS worked closely with GE engineering personnel to understand the application and design upgraded screw feeders and conveyors to replace existing equipment. KWS designed the new screw feeders to mate to the existing storage bins and fit into the current plant layout. Our knowledge of bulk material handling applications ensured that the project would be a success. KWS designed five different screw feeders to accurately meter the raw materials from the storage bins to the weigh hopper.
Special Features
KWS provided five heavy-duty carbon steel screw feeders of various lengths to fit within the existing plant configuration. For each screw feeder, the inlet was flared to match the existing storage bin outlet dimensions and transitioned to a non-split tubular housing. The housing assembly was constructed as one weldment to eliminate any issues with product or dust leakage. KWS provided end shafts with special bronze bushings on the tail end to reduce maintenance and downtime. Since the weigh hopper was on load cells, the screw feeders could not be directly bolted or attached to the weigh hopper. Special transitions at the discharge end of each screw feeder allowed the raw materials to discharge into the weigh bin without affecting load cell readings. Each screw feeder was isolated from the weigh bin to ensure complete accuracy of the batch. The expertise, communication and teamwork by both parties over the duration of the project were an important part of its success.
Testimonial
"I am very satisfied with KWS and have used them for at least two separate projects. If I have further needs for this type of equipment, KWS will certainly be on my bid list."
Steve Hutchins, Project Manager – GE Consumer & Industrial