KWS Provides Screw Feeder to Nikkei Aluminum for Recycling
General Description
Aluminum is a vital component in our everyday lives and is used in everything from vehicles to construction, electronics, and a multitude of other applications. Aluminum is one of the most recycled materials in use today and it can be recycled directly back into itself. Most of all the aluminum produced is still in use today, thanks to recycling. Over 90-percent of the aluminum used in automotive and construction industries has been recycled.
Nikkei Aluminum is a secondary aluminum manufacturer that melts down recycled scrap aluminum to produce ingots for automotive wheels, master cylinders, garden tools, and many other products.
Nikkei Aluminum and KWS partnered to design a hopper and screw feeder for loading and metering recycled aluminum chips to a smelting furnace. KWS provided a hopper that worked easily with a front-end loader and a screw feeder to meter the material, all within defined space constraints.
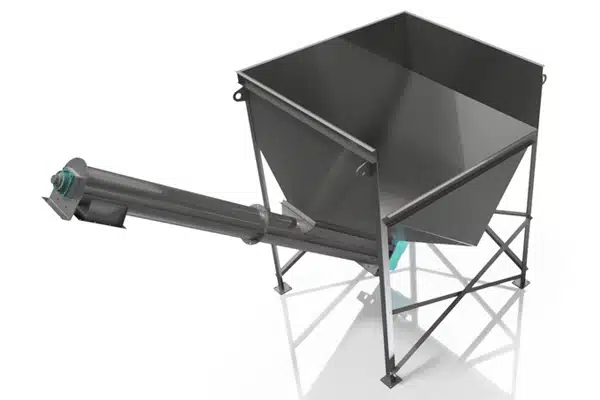
Aluminum Chips are Loaded into Hopper with Frontend Loader
Design Parameters
- Product Type: Aluminum Scrap Chips
- Material Density: 40 Lbs. per Cubic Foot
- Capacity: 150 Cubic Feet per Hour
- Duty: 24 Hours Per Day, 7 Days Per Week
KWS Advantages
KWS made several trips to the Nikkei plant in Columbus, IN to collaborate with their engineers and solve the storage and metering problem. Existing equipment was unreliable and causing loss of productivity. KWS provided a new hopper and screw feeder that was reliable and easy to maintain.
KWS used 3D modeling to make sure the hopper could handle the volume of material from the front-end loader without causing maneuverability issues. Our extensive knowledge of bulk materials allowed us to understand material flow properties so we could design a screw feeder that would operate continuously without complications.
KWS Special Features
Aluminum chips are abrasive, so KWS constructed the flights from AR400 abrasion-resistant material. Variable pitch flighting ensures accurate metering of aluminum chips to the smelting furnace. The screw feeder housing was split tubular to improve metering efficiency and for ease of clean out without fully disassembling the unit.
A KWS bulkhead trough end provided a standoff between the trough end and drive unit to protect the drive from contamination. The direct-shaft mount drive unit is compact and a cost-effective alternative to a traditional belt-driven screw conveyor drive.
The hopper provided enough volume for at least two bucket loads from the frontend loader and was re-enforced to handle any rough treatment from the equipment operators.
Testimonial
"KWS came through for us. The screw feeder is working as designed. Also, thank you for the back-up screw feeder."
Van Anthony, Plant Manager – Nikkei Aluminum
Hopper is Designed to Withstand Abuse
Variable Pitch Flighting Accurately Meters Aluminum Chips to Smelting Furnace
Bulkhead Trough End Protects Drive Unit from Contamination