KWS Provides Biosolids Loadout System for Myers Water Treatment Plant
H.E. Myers Water Treatment Plant Solids Handling Facility
Mobile, AL
General Description
The Mobile Area Water and Sewer System (MAWSS) provides safe drinking water and sanitary sewer services to areas in and around Mobile, AL. MAWSS came into being in 1968 when the Mobile Water Service System and the Board of Water and Sewer Commissioners merged together. Today, water is delivered from the 3,600-acre lake and pumping station by pipes to two reservoirs where it is diverted either to domestic or industrial use. Approximately 60 million gallons per day of water is pumped through the S. Palmer Gaillard Pumping Station and transmitted by two water treatment facilities.
The H.E. Myers Water Treatment Facility is permitted to process 30 million gallons per day. The facility is currently over 30 years old and is being completely modernized. KWS provided new conveying equipment for a dewatered biosolids truck loadout system.
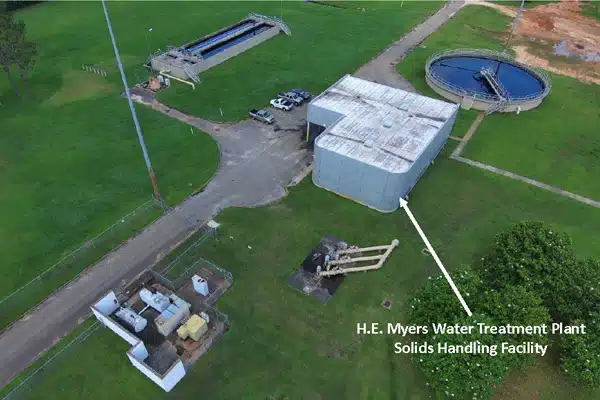
Myers Solids Handling Facility is Located in Mobile, AL
Design Parameters
- Product Type: Dewatered Biosolids
- Material Density: 45 to 65 Lbs. per Cubic Foot
- Capacity: 593 Cubic Feet per Hour
- Duty: Intermittent
KWS Advantages
KWS was selected to provide a loadout system that required minimal operator involvement. Working closely with the consulting engineer, and contractors, KWS designed a system that met the requirements of the process and fit in the very confined space at the plant. KWS utilized the latest 3D CAD modeling techniques to model the complete system to help the engineer determine equipment and structural support locations. KWS also worked closely with Andritz to ensure the interface between centrifuges and conveyors fit up properly. Structural supports for the new load out system were analyzed, approved, and stamped by a professional engineer certified by the state of Alabama. As a result, the installation phase went very smoothly. KWS assisted the contractor during the installation, commissioning, and start-up phases to ensure the system was installed in accordance with the consulting engineer’s design.
Trucks are Loaded Out with Dewatered Biosolids
KWS Special Features
KWS selected a shaftless screw conveyor system to convey and elevate the sticky and wet biosolids. KWS shaftless spirals are the strongest and toughest in the industry and guaranteed for many years of uninterrupted operation. KWS shaftless conveyors are equipped with heavy UHMW liners to handle wear and abrasion. All exterior components of the conveyors, diverter chutes and structural supports were manufactured from 304 stainless steel to prevent corrosion.
KWS Shaftless Screw Conveyors always include our exclusive one-piece flanged drive shaft. The drive shaft is machined from solid bar stock and is guaranteed for life. To protect the equipment and operators, each shaftless screw conveyor was fitted with an emergency pull cord safety stop system, motion speed sensor, and fixed covers secured with safety bolts requiring a special tool to remove allowing only trained maintenance personnel to access the equipment.
KWS provided specially designed electrically actuated Y-style diverter chutes to direct the flow of the dewatered biosolids from the centrifuges into two shaftless conveyors. KWS supplied local remote hand stations for all diverter chutes for easier access to the controls. The diverter chute is equipped with a UHMW lined diverter plate to prevent clogging and increase flowability.
Rigid intermediate chutes were installed between conveyors for easy material transfer. The chutes were lined with low-friction UHMW to increase flowability and avoid bridging from occurring. The rigid chutes are designed with bolted on inspection doors for access by maintenance personnel only.
Andritz Centrifuges Discharge Dewatered Biosolids to KWS Loadout System
Biosolids are Diverted to Redundant Loadout Systems
Electric Gate Actuators are Operated from Main Control Panel
Transfer Screw Conveyors Receive Dewatered Biosolids from Centrifuges
Dewatered Biosolids are Transferred to Inclined Screw Conveyors
Emergency Safety Pull Cord Stop System is Installed on Every Conveyor
Redundant Conveyors are Located Side-By-Side
Rigid Chutes Connect Transfer Screw Conveyors to Inclined Screw Conveyors
Inclined Screw Conveyors Elevate Biosolids to Loadout Area
Platform Supports Inclined Screw Conveyors and Provides Access for Maintenance