Hollow Flight Thermal Processor for Heating Rubber Powder
General Description
Micronized rubber powders (MRP) are versatile raw materials that replace oil and rubber-based feedstocks in a wide range of applications including high performance tires, industrial rubber, consumer and industrial plastics goods, asphalt, coatings, and construction materials. MRP deliver product performance, lower production costs and reduced waste by transforming end of life tires and other post-industrial rubber into micron scale powders.
By using MRP, end users improve their products and provide an environmental benefit to society. Adding MRP eliminates waste that would otherwise go into landfills, helping reduce the need for oil-based feedstocks, saving energy and reducing greenhouse gases.
Design Parameters
- Product Type: Rubber Powder
- Product Inlet Temperature: -90°F
- Product Outlet Temperature: 80°F
- Material Density: 30 Lbs. per Cubic Foot
- Conveyor System Capacity: 267 Cubic Feet per Hour
- Duty: Intermittent
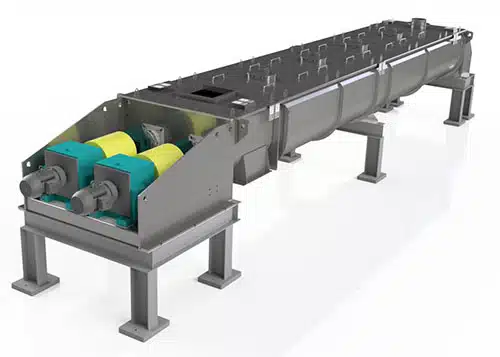
KWS Twin Thermal Processor Heats MRP from minus 90 to above 80-Degrees F
KWS Advantages
Engineers at KWS designed a thermal processor based on the customer’s required volumetric capacity and necessary heating requirements. The KWS hollow flight design provides a path for heating media to flow through the full length of the screw flights delivering maximum surface area for heat transfer. Additionally, the center pipe and jacket around the trough also provide additional surface area for heat transfer. The combined surface area heats MRP from minus 90 to greater than 80-degrees F.
KWS Special Features
The KWS thermal processor was constructed from 304 stainless steel due to the demands of the application and internal pressure requirements. Twin-hollow flight screws were selected to handle the heat load and conveying conditions. KWS thermal processors are designed in strict accordance with the ASME Boiler and Pressure Vessel Code. As an ASME certified pressure vessel manufacturer, KWS provided an ASME code stamp for the trough jacket and hollow flight screws.
Each hollow flight screw is driven by an individual drive unit supplying system redundancy and maximum heat transfer efficiency. Drive units and bearings are located away from the heat source and operate at ambient temperature. Dual-pass rotary unions provide a pathway for the heat transfer media through each hollow flight screw.
KWS utilized a twin slider base pedestal trough end to protect the end bearings from contamination and allow for thermal expansion due to the high temperature of the heating medium. Expansion and contraction are common in every high-temperature application and occur axially along the length of the screw and trough. The KWS slider base style trough end is designed for thermal expansion and can account for axial expansion up to 4 inches.
Testimonial
"The KWS thermal processor works great! We plan to purchase another unit soon. Thanks for your excellent engineering and overall product quality."
Process Engineer
Dual-Pass Rotary Unions Provide Pathway for Heat Transfer Media
Twin-Hollow Flight Screws Handle Heat Load
Hollow Flight Design Delivers Maximum Surface Area for Heat Transfer