Heavy-Duty Bucket Elevator to Lift Char Created from Pyrolysis Process
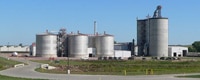
Vadxx Energy
Akron, OH
General Description
Vadxx Energy is a high tech recycling company that converts recyclable and non-recyclable plastic into higher value energy products. The Vadxx process heats waste polyolefin products — certain kinds of plastics — in a controlled way, without using catalysts; a process called pyrolysis. The heat slowly melts and condenses the plastics, turning them back into carbon and hydrogen components. The majority of the plastics waste — about 75% to 80% — gets turned into hydrocarbon liquid, which can be used to make products like diesel fuel. The Vadxx plant can process about 20,000 tons of waste a year, producing about 80,000 barrels of fuel. Another 5% becomes a non-hazardous byproduct called char and the rest becomes gas that is used to heat the process. For this project, Vadxx Energy required a bucket elevator to elevate char after it was cooled by a screw thermal processor to a bulk bag filling machine.
Design Parameters
- Product Type: Char (dry, free-flowing)
- Material Density: 29 Lbs. per Cubic Foot
- Capacity: 57 Cubic Feet per Hour
- Duty: 24 Hours per Day, 7 Days per Week
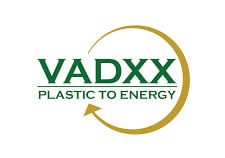
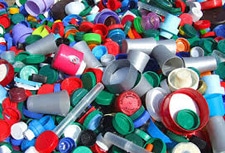
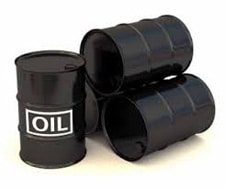
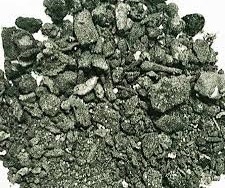
KWS Advantages
The engineering firm on this project was Rockwell Automation, the world’s largest company dedicated to industrial automation. Rockwell had previously contacted KWS back in 2012 for engineering assistance on the project. Some general dimensions and requirements were given and KWS designed the rest of the solution.
Rockwell understood the plant automation process but needed help designing the material handling system for the process, so they naturally came to KWS. KWS provided a competitively designed bucket elevator that was delivered within the time constraints of the project. KWS utilizes lean concepts throughout the sales, engineering and manufacturing processes, making the time constraints of the project a non-issue.
Special Features
A thermal processor cooled the char and fed the bucket elevator at a controlled rate. The heavy-duty bucket elevator elevated the char approximately 30-feet and discharged it to a bulk bag filling machine. Since the char is not a tremendously harsh product, a belt-type bucket elevator with nylon buckets was selected by KWS. KWS also designed a special head take-up section since maintenance access was limited in the boot section. KWS was a partner to Rockwell Automation and helped resolve key issues with equipment interfaces and process function.
KWS designed the discharge chutes to take the cooled char from the thermal processor to the bucket elevator as well as the chutes from the bucket elevator to the bulk bagging machine. KWS worked with the installation contractor to quickly answer any questions that came up during the equipment installation. KWS made the bucket elevator dust-tight to contain the char dust. KWS split gland seals are used on all bucket elevator shafts as a standard and provide superior leakage protection. All KWS equipment is modeled in Autodesk 3D Inventor, which made changes during the engineering phase easy to make.