Expedited Delivery Keeps Carmeuse Lime Operating
General Description
Limestone is a versatile material mined in many parts of the world. Commonly used in crushed form as a construction aggregate and filler product in roofing shingles, limestone can also be heated to create a number of lime materials used in wastewater treatment, flue gas treatment, and pulp and paper.
As a leader in the lime and limestone market, Carmeuse can’t afford downtime. When a plant discovered a critical screw conveyor had not been ordered for the upcoming outage, options were limited. Other screw conveyor manufacturers were not capable of providing a solution in time for the outage. KWS stepped up to deliver the necessary equipment on site in time for Carmeuse’s installation window.
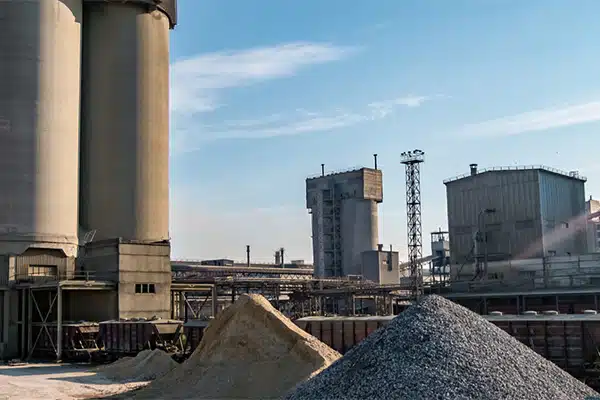
Carmeuse Lime Produces Lime and Limestone Products
Design Parameters
- Product Type: Crushed Limestone
- Material Density: 85 to 90 Lbs. per Cubic Foot
- Capacity: 2,415 Cubic Feet per Hour
- Duty: 24 Hours per Day, 7 Days per Week
KWS Advantages
With only two weeks until the install window, KWS manufactured, assembled, and delivered a complete screw conveyor to the plant in Saginaw, AL. Due to application requirements, all components were heavy-duty and custom manufactured. Typical lead time would be 6 to 8 weeks from any other manufacturer. KWS shipped a complete screw conveyor in just 9 working days after first receiving the opportunity. Even with limited time, KWS did not sacrifice quality as every component underwent comprehensive QC inspections and the fully assembled screw conveyor was successfully tested at KWS facilities before shipment in accordance with KWS standard procedures.
KWS Special Features
As a critical part of the process, the screw conveyor required a robust design. Screw flights were made of AR400 plate to resist wear and ensure a long life at full conveying capacity. Oversized schedule 80 pipe and bolt pads were utilized to withstand the potential full motor torque available from the 20-horsepower drive package. By designing for full motor torque as opposed to normal operating torque, KWS eliminated any potential for catastrophic failure.
Testimonial
“KWS really got us out of a bind, the old conveyor was about to fail, and we can only get at it during a scheduled outage. Our only other option was to reschedule the outage and hope the screw conveyor would last, but it could have shut the entire plant down.”
Plant Maintenance Manager – Carmeuse Lime
New KWS Screw Conveyor was Heavy-Duty with AR400 Flights
Screw Conveyor is Critical to Plant Operations