Custom Drag Conveyor for Hot Pellets in Cargill Animal Feed Plant
General Description
Cargill is one of the largest producers of animal feed products in the world, generating over 20 million tons of feed per year. Cargill feed products support livestock production that ultimately touches the plates of more than one billion people every day.
Cargill Animal Nutrition in Ogden, Utah required a custom replacement drag conveyor to handle hot pellets fed directly from their pellet mill. The existing equipment was located within a highly confined area, making the outer dimensions of the replacement drag conveyor critical. The pellets also needed to be conveyed downstream while maintaining their shape and avoiding damage. KWS designed and engineered a long-lasting custom conveying solution for Cargill.
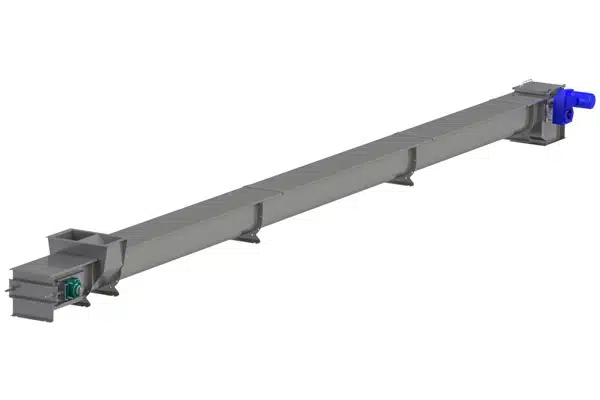
New KWS Drag Conveyor Transfers Hot Pellets from Pellet Mill to Further Processing
Design Parameters
- Product Type: Hot Pellets
- Material Density: 40 Lbs. per Cubic Foot
- Capacity: 24,000 Lbs. per Hour
- Duty: 24 Hours per Day, 7 Days per Week
KWS Advantages
With the experience of ten degreed mechanical engineers, KWS supplied the right solution and delivered ahead of schedule. KWS provided an onsite survey to assess existing equipment and offered 3D-modeled approval drawings of the entire drag conveyor assembly. A drag conveyor suits this application because the paddles gently push the pellets without degradation, which is important for further processing. The existing drag conveyor had issues with the UHMW paddles warping over time due to the heat of the pellets. The chain also had a significant amount of rust which impacted product integrity and flowability. KWS provided an improved drag conveyor design that will last Cargill for many years.
Stainless Steel Chain with TIVAR® H.O.T UHMW Paddles Easily Handle Elevated Operating Temperature
KWS Special Features
KWS improved the design by using stainless steel chain and TIVAR® H.O.T UHMW for the paddles. TIVAR® H.O.T. UHMW excels where temperatures range up to 275-degrees F, nearly 100-degrees F higher than competing UHMW-PE formulations. TIVAR® H.O.T. will last up to 10 times longer in higher temperature environments and has excellent wear and release characteristics.
Stainless-steel chain was better equipped to handle the moisture and heat of the pellets. The complete conveyor was constructed from 304 stainless steel construction to eliminate corrosion and facilitate easy washdown. A beltless motorized drive was selected to prevent moisture related, v-belt slippage. The drag conveyor was shipped fully assembled and shop tested to ensure an issue-free installation on site.
Testimonial
"The solutions KWS provided have been working great! The improvements made the plant extremely happy."
Jared Scholes, Account Representative – MiMotion
304 Stainless Steel Construction Eliminates Corrosion
Beltless Drive Unit Improves Efficiency and Reduces Maintenance