Conveying Pecans with Food Grade Screw Conveyor
General Description
Confections and snack foods are a staple of American culture. The average American consumes three or more snacks per day with an annual spend totaling over $180 billion. With pressure from consumers to deliver these delectable delights, new product development is a continuous process.
One of the world’s largest confectionery companies, with annual sales of upwards of $20 billion, specializes in making chocolate-flavored snacks. With snacks rising in popularity in recent years, the end user developed a new pecan-filled chocolate bar snack. KWS provided a food grade screw conveyor to help with their new production line needs.
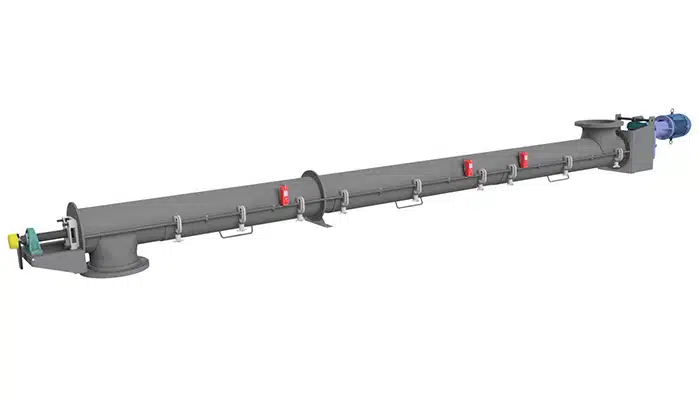
Split Tubular Housing Allows for Easy Cleaning
Design Parameters
- Product Type: Pecans
- Material Density: 30 Lbs. per Cubic Foot
- Conveyor System Capacity: 229 Cubic feet per Hour
- Duty: Continuous
KWS Advantages
The KWS and system integrator’s sales and engineering teams collaborated to ensure the new production line would be successful. KWS works with every major food manufacturer and supplies conveying systems to many plants across the US. For this specific application, KWS designed and manufactured a 9-inch diameter screw conveyor to move pecans from a volumetric feeding device to be deposited into a continuous mixer to be mixed with other major ingredients before discharging to the candy-making machine.
KWS Special Features
For the screw conveyor, KWS utilized a split tubular trough housing for easy accessibility to the internal components for daily cleaning. The design also incorporated hinged and clamped drop-bottom doors as the conveyor would be installed at an elevated location. Because safety is a primary concern in manufacturing facilities, KWS utilized safety interlock switches with actuator key design mounted to the leading edge of drop-bottom doors. The design provides positively operated switching contacts and a tamper-resistant actuator mechanism to de-energize the screw conveyor when a door is opened.
Since pecans are a food product, no pits or crevices can be present on the internal surfaces of the screw conveyor. Standard CEMA bolted shaft connections are not allowed. Instead, the shafts were shrink-fit, and seal welded to the screw centerpipe. KWS torque arm trough ends are ideal when the drive shaft is welded into the screw. Since the shaft mounted gear reducer is allowed to “float” on the drive shaft, any stress caused by the rigid welded connection is eliminated.
Mechanical shaft seals prevent pecans from leaking from the drive and tail shaft penetrations of the screw conveyor. KWS chose to use Woodex/MECO HB shaft seals for this application. The HB model’s sealing performance can be easily monitored by maintenance and production personnel using the seal’s pressure gauge system. The pressure gauge system is effective in quickly alerting maintenance and production personnel of a potential seal breach so that repairs or replacements can be made before product leakage occurs. MECO seals are fully repairable with internal components easily accessible for cleaning and maintenance.
Testimonial
"KWS quality is always outstanding. We have several KWS screw conveyors in multiple facilities in the US. We will continue to use KWS for all future production and line expansions."
Production Manager – Snack Food Manufacturer
Screw Conveyor Conveys Pecans for Snack Food Manufacturer
KWS Torque Arm Trough End Eliminates Stress on Drive Shaft
Mechanical Shaft Seals Prevent Bulk Material Leakage
Safety Interlock Switches De-Energize Screw Conveyor When Door is Opened