Biosolids Loud Out for Dewatering and Disinfection Conveyor System Manitou Drive Dewatering Facility in Kitchener, Ontario, Canada
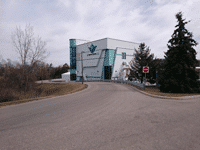
Manitou Drive Dewatering Facility
Kitchener, ON
City of Waterloo
Waterloo, ON
Hydromantis, Inc.
Engineering Consultant - Beasley
Hamilton, ON
Graham Construction
Mississauga, ON
General Description
The regional municipality of Waterloo treats about 45 million gallons of wastewater each day and with increasing population in the region, the figure is expected to grow. In response to this, the Region recently undertook a large capital improvement program to improve and expand its wastewater treatment capabilities at the Kitchener Wastewater Treatment Plant.
The multi-phased project entailed constructing a new biosolids dewatering facility, refurbishing the secondary treatment processes at Plant 2, constructing a new ultraviolet disinfection facility and effluent pumping station and a large capacity biosolids storage and truck loading facility. The Kitchener Wastewater Treatment Plant could then decommission its bio¬solids lagoons, a major source of odor and an inefficient use of scarce land.
Graham Construction was responsible for the new biosolids dewatering facility and any work at the existing Kitchener Waste¬water Treatment Plant that ties into the new facility. The two-story, 15,500-square-foot biosolids dewatering facility contains equipment that separates liquid and solid waste as one of the stages of the sewage treatment process. The liquid waste will travel via underground pipe back to the Kitchener Wastewater Treatment Plant for treatment. The solid waste (biosolids) is transferred across the facility through a shaftless conveyor system to tractor-trailers that haul the material to farmers’ fields.
Design Parameters
Parameter | Distribution Conveyors | Transfer and Truckloading Live Bottoms | Silos |
---|---|---|---|
Volume – m3/hr: | 18 m3/hr | up to 80 m3/hr | 90 tons each (270 tons total) |
Density: | 800-1000 kgs/m3 | 800-1000 kgs/m3 | 800-1000 kgs/m3 |
Dry Solids: | 25-32% | 25-32% | 25-32% |
KWS Advantages
KWS fully participated during design and development stages of the project. Since KWS is capable of engineering and manufacturing all type of conveyance equipment, storage vessels, unloading systems and slide gates, we could ensure that the solution provided the best and most reliable performance for the intended purpose.
KWS designed, manufactured and provided full commissioning support for an integrated system which required expertise with –
- Process Conditions
- Design and fabrication of silos, screw conveyors, slide gates, chutes, and support structures
- Application engineering of instrumentation, motion sensors, level sensors, weigh system, overload protection, truck position sensors
- Design of PLC based controls with touch screen OITs
The system included over 600-feet of 20-inch diameter shaftless screw conveyors which had to be designed into both existing and new buildings. KWS utilized their extensive experience with 3D modelling to ensure that the equipment fit into the limited space and correctly spanned from the new to existing building structures.
Special Features
KWS provided fully redundant systems from the centrifuges to the truck loading bays with two distribution conveyors to distribute dewatered biosolids cake from any centrifuge to any of the three silos. A diverter gate was used to direct the biosolids and was essential that conveyor availability was maximized. Biosolids were evenly drawn from the storage silos using shafted live bottom screw feeders. The live bottom screw feeders were designed in pairs so that the discharge rate could be incremented by thirds of the total capacity. The KWS shaftless vertical conveyors were among the highest capacity in North America and operate efficiently over a wide range of solids content produced by the centrifuges.
A PLC based control system with fault detection and dynamic path reconfiguration further improved the overall process. In the event of a fault was detected, the control system assessed whether an alterative path was available and reconfigured the distribution conveyors without interruption of the centrifuge operation. Trucks are guided into the truck bay using traffic lights which use proximity sensors to position the trucks. Gates are opened and closed to provide an evenly distributed load into trucks using information from the Bin weigh system and level sensor systems.
Testimonial
"The system works great and requires very little attention to operate and maintain."
Joel Muir, Project Manager – Ontario Clean Water Authority