KWS Emergency Services Provide Solution For Breakdown
General Description
One of the world’s leading makers of building products, Georgia Pacific needed emergency service. A large 20-inch diameter by 27-foot-long screw conveyor required very custom machine work and a corresponding drive shaft manufactured in expedited fashion. KWS provided the solution in less than 18 hours.
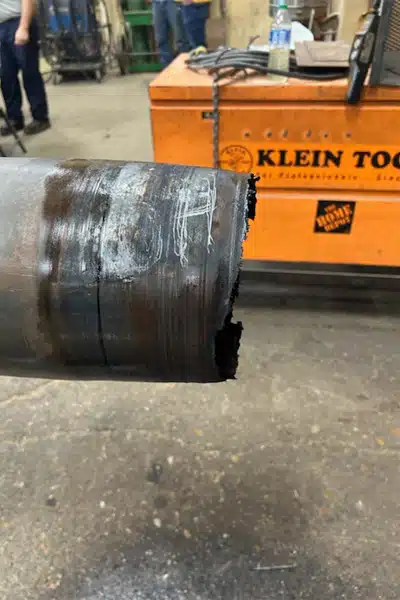
Existing Screw Failed Due to Corrosion and Wear
Challenge
An existing screw conveyor at the Lufkin, Texas plant had failed due to corrosion and wear. Compounding the problem was that the center pipe of the screw had a seal welded taper style bushing inside of it that secured the driveshaft in place. The center pipe of the screw had to be cut down five inches to establish quality, full strength material and a new custom driveshaft machined from strong 4140 alloy material. After manufacturing, precision straightening with a total indicated run out (TIR) of 0.010-inches was required.
KWS Advantage
KWS provides same day emergency services for its loyal distributors and customers. Working cohesively and effectively, a plan was developed and followed to perfection. With a five-hour time and distance factor from plant to plant, the plan required precision timing. A local and trusted service provider within minutes of the Georgia Pacific plant was able to cut the pipe and seal weld the taper bushing back in place. Meanwhile, KWS created an engineered blueprint of the modified drive shaft that was converted from an infield hand sketch. KWS immediately began machining a new drive shaft. Simultaneously, the modified screw was in route to KWS. Upon arrival of the screw and completion of the driveshaft, KWS straightened the screw in a precision lathe to within 0.010-inches TIR. Quality Control verified the TIR readings, drive shaft dimensions and approved the immediate return of the screw to be put right back in service.
Cost Savings
With an elapsed time of approximately eighteen hours versus a normal lead time of five days (120 hours), a very, very conservative cost savings of $100,000 was easily realized by the customer.
Testimonial
"Thank all of you for the service over the weekend, this will get us back in operation. We will be ordering a new KWS screw for this line."
Sherman Thomas, Maintenance Manager – Georgia Pacific
Completed New Drive Shaft and Repaired Screw on Hot Shot Back to Georgia Pacific Plant