Passivation, Pickling, and Electropolishing
Stainless steel surface treatment and finishes are very important for many bulk material conveying applications. Food products, specialty chemicals, and even environmental industries may require a specific surface treatment or finish to keep a bulk material from contamination or spoilage.
Pickling, passivating, and/or electropolishing remove impurities, stain, rust, and scale so the stainless steel has improved corrosion resistance and a homogeneous surface. Each level of surface treatment or finish has its own benefits.
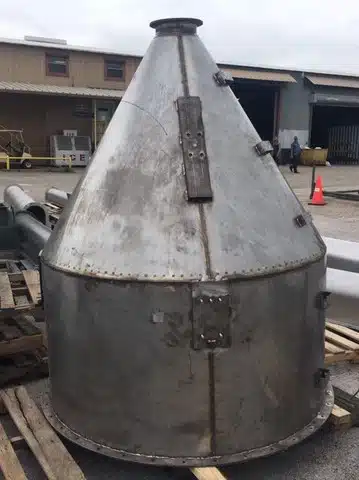
Hopper Before Passivation with Impurities, Stains, and Scale
Features
Passivation – Passivation is a surface treatment with nitric acid that dissolves corrosion-susceptible free iron, nonmetallic inclusions, and other surface contaminants. Stainless steel will naturally passivate when a clean surface is exposed to an environment with enough oxygen to form a chromium-rich oxide surface. This increases the corrosion resistance of stainless steel and doesn’t affect the metal’s appearance. No metal is removed during the passivation process.
Pickling – Pickling is the cleaning of a metal surface where actual metal removal is used to remove heavy oxide films. An acid solution (hydrochloric or sulfuric acid) is applied to the material to remove weld scale or heat tint from the material. Pickled stainless steel is free from surface carbon steel contamination and the embedded iron particles but it is left dull and has a matte gray finish.
Prior to pickling, the material is cleaned of all foreign substances. Stainless steel can be cleaned using a multitude of mechanical or manual methods including alkaline/solvent cleaners, ultrasonic cleaning, or high-pressure cleaning. The acid solution is then applied to the stainless steel component via tank immersion, circulation, spraying, or using gel.
Electropolishing – Electropolishing smooths and polishes stainless steel surfaces. The component surface must have a 150-grit finish before electropolishing. Electropolishing results in a metallically pure surface, an unaffected basic structure, with improved corrosion resistance and permanently shiny surface.
Benefits
Passivation – Passivation removes surface contaminants without the loss of surface material. Material surface finish is not affected by the acids used for cleaning.
Pickling – Pickling provides a uniform finish and color with the removal of heavy oxide film, weld scale, and heat tint. Material surface finish is a matte finish.
Electropolishing – Electropolishing is used for sanitary and food grade applications along and for conveying sticky and corrosive bulk materials. The smooth and polished surface helps keep material from sticking. Equipment can be easily washed down.
Pickling Removes Weld Scale and Heat Tint and Leaves Dull Gray Matte Finish
Electropolished Screw Surfaces are Smooth and Shiny
Hopper After Passivation with Impurities Removed and Clean Finish