Redesigned Screws Increase Uptime and Reduce Cost for Honeywell Specialty Materials
General Description of the Application
Honeywell Specialty Materials is a chemical plant located at Geismar, LA approximately 60 miles west of New Orleans on the East Bank of the Mississippi River. The plant manufactures various chemical products including a non-ozone depleting blowing agent used in the production of rigid foam insulation, a non-ozone depleting refrigerant, and hydrofluoric acid.
Screw conveyors are located at the discharge of four rotary furnaces to convey spent chemicals used in the manufacturing process. The chemical residue is very corrosive when combined with moisture. The screw conveyors must be designed to withstand temperatures up to 700-degrees F and high acidity. Honeywell has each of the six rotary furnace screw conveyors set up on a 6-month replacement schedule to prevent unscheduled down time. The existing screws were failing prematurely and Honeywell could not tolerate the downtime. Working together, KWS and Motion Industries provided a better solution that reduced downtime and saved Honeywell money.
Design Parameters of Application
- Product Type: Abrasive Hot Acid Residue Powder
- Material Density: 90 Pounds per Cubic Foot
- Conveyor Capacity: 4 Tons per Hour
- Moisture Content: 10 to 15-Percent
- Duty: 24 Hours per Day, 7 Days per Week
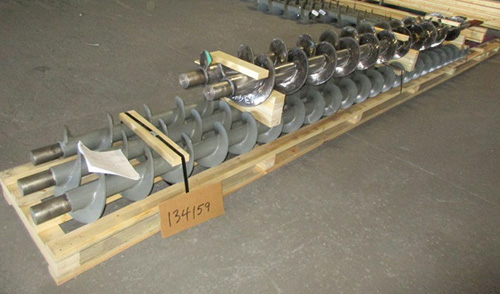
New KWS Screws are Ready for Shipment
Advantages Provided by KWS
A team from KWS and Motion Industries visited the Geismar facility and met with the Honeywell Plant Superintendent to determine the exact needs of the plant. While onsite, the KWS team gathered dimensional information from the existing equipment and recommended a design which would handle current requirements and provide significant cost savings to Honeywell. Based on all the information gathered, KWS redesigned the rotary furnace discharge screws and provided in excess of 30-percent cost savings when compared to their previous supplier.
Special Features of KWS Design
Based on material testing and new calculations, KWS redesigned the rotary furnace discharge screws with a larger diameter center pipe and heavier wall thickness to withstand torsional and bending loads at elevated temperatures. A high-nickel alloy Hastelloy sleeve was added to the drive shaft in the area of high wear and corrosion. Hastelloy has excellent corrosion-resistant properties at high temperatures. The flights of the screw were continuously welded on both sides to the center pipe for added strength and then hard surfaced with Postalloy on the carrying side and periphery of the flights. Postalloy hard surfacing material has excellent abrasion resistance. KWS straightened each screw to within 0.015-inches Total Indicated Runout (T.I.R.) to eliminate any movement in the drive assembly.
Testimonial
"KWS and Motion Industries have provided true savings along with a quality product to Honeywell over our previous supplier. KWS and Motion Industries have been very responsive to our requests to modify our original design which has further increased the durability and optimized our screws’ performance."
Chris Leonard Reliability Engineer, Rotating Equipment – Honeywell Specialty Materials
Existing Screws Show a Large Amount of Corrosion and Wear
Existing Screws were Mounted on Smaller Center Diameter Pipe