Shafted Screw Conveyor for Conveying Biosolids Egan WRP (Chicago)
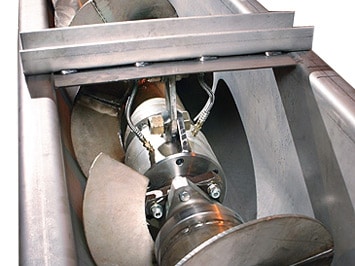
Metropolitan Water Reclamation District of Greater Chicago
Chicago, IL
Metropolitan Water Reclamation District of Greater Chicago
Chicago, IL
IHC Construction Companies, LLC
Elgin, IL
Egan Waste Reclamation Plant
Schaumburg, IL
General Description
The Metropolitan Water Reclamation District of Greater Chicago is an independent government and taxing body which serves an area of 883 square miles and includes the City of Chicago as well as 125 suburban communities. The District serves an equivalent population of 10.35 million people; 5.25 million residential customers, a commercial and industrial equivalent of 4.5 million people and a combined sewer overflow equivalent of 0.6 million people.
In conjunction with its biosolids beneficial utilization and farm land application program, the District recycles all biosolids in land application programs in northeast Illinois, and owns over 13,500 acres of land in Fulton County, Illinois, formerly used for biosolids application.
KWS Environmental participated in the latest plant improvement project; 06-494-3P – Centrifuge Building and Sludge Loading System Upgrades, EWRP and HPWRP by designing and manufacturing the screw conveyor equipment associated with this project.
The objectives of this project included; replace existing conveyor system with new system, increasing efficiency by reducing number of outages (reduce the number of outages from the 2012 – 2014 average of 10 total and 6 unscheduled) and lowering maintenance costs (2009 – 2012 average conveyor cost of $76,000). Increase dewatered biosolids storage capacity to allow for longer uninterrupted periods of centrifuge operation (from 19 hours five days per week to 24 hours six days per week).
Design Parameters
- Material: Dewatered Biosolids
- Solids Content: 13 to 30-percent by weight
- Material Density: 62 to 70-Lbs. per Cubic Foot
- Maximum Design Capacity: 500 Cubic Feet per Hour
- Duty: 24 Hours per Day, 7 Days per Week
KWS Advantages
The space available was very limited requiring a custom designed shafted screw conveyor and slide gates that met the dimensional requirements of the building and interfacing equipment. The expertise that KWS has with 3D modeling using Autodesk Inventor ensured that the equipment fit exactly to the Customer’s requirements. Installation was accomplished quickly and efficiently which allowed the Contractor to deliver on time and to budget.
Reliability was essential as a project objective to reduce maintenance costs and unscheduled outages. Despite redundant centrifuges before the conveyor and pumps and storage silos after the conveyor, there is only one screw conveyor. Also, the plant maintenance costs on the existing conveyors averaged over $76,000 per year. Quality and reliability meant that KWS, the only ISO 9001 certified screw conveyor manufacturer in North America was the only logical choice.
KWS is one the largest screw conveyor manufacturers in the U.S and has a huge installation base of screw conveyors. With over 45 years of knowledge and experience to apply to environmental applications, KWS knows how to design and manufacture screw conveyors that will operate trouble-free for many years.
KWS supported the installation, commissioning and training by providing a qualified and registered engineer familiar with the project, design requirements and equipment delivered.
Special Features
KWS supplied a shafted screw conveyor with KWS Tor-Ri-Flex sealed intermediate bearing assemblies. The KWS Tor-Ri-Flex intermediate bearing is designed to handle angular misalignment and includes two low friction bearings to support radial loads. The bearings are sealed against contamination and are constantly purged with grease. Each screw section was mounted on a large-diameter heavy duty center pipe that allowed for 16-foot long spans so that the number of intermediate bearings required was minimized. The bearings are located at accessible points and can be maintained without disrupting adjacent screw sections.
Routine lubrication is achieved automatically using spring-actuated lubrication pots which can be replaced without tools. Should major maintenance be required, the bearing assembly can be removed without interrupting the adjacent screw sections.