Improving Recycling in Poultry Processing
Poultry Times — July 2, 2020
By Jim Collins & Keith Sandlin
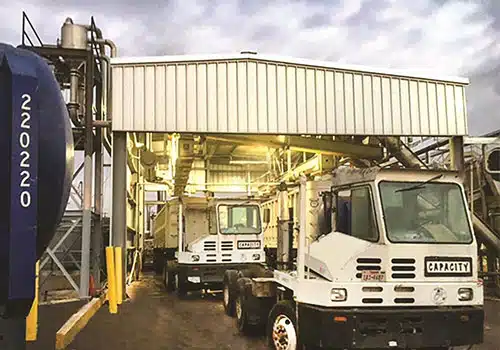
Screw conveyor load out system
BIRMINGHAM, Ala. — A consistent flow of byproducts away from the poultry plant and to the rendering facility is critical to efficiency and reduced downtime. Losing the capability to transfer the inedible byproducts to the rendering facility can have a major impact on production and profitability.
There are many methods that plants can use to move this byproduct. The majority of the modern facilities use screw conveyors to accumulate, transport and load trucks for offsite rendering. In many instances however, the flow of product has to continually stop and start in order to wait for loadout trucks.
One way to avert this “stop and start” issue is with a “state-of-the-art” offal and feather loadout system (Image 1); the right one can be the answer if the design makes sense for the plant’s specific needs (environment, etc.), and with proper preventive and regular maintenance.
Time is Money
First, let’s consider some numbers. Each poultry plant – large and small – is a critical contributor to this important industry, which produces healthy, high-quality food products for consumers all over the world. More than 10 billion chickens and turkeys are processed annually in the United States. Now consider the transfers. The average poultry plant processes millions of pounds per week of edible meat for human consumption and a comparable amount of inedible by-products that need to be further processed or “rendered” for use in animal feed and many other products.
No part of a bird is wasted. Once the edible portions have been separated by evisceration, feathers and offal are sent to the rendering plant. Offal refers to internal organs and entrails of a butchered animal. Offal is cooked, ground, and further processed at a rendering plant, producing material used for fertilizer, fuel, or as a protein meal additive for animal feed and pet food. Feathers are processed into feather meal and result in a very high-density source of protein for animal feed and pet food.
Time is a critical factor in handling and processing offal. To produce the highest quality feed, rendering plants must receive offal within eight hours from the time the bird was processed. The composition of the meat degrades rapidly in the first 24 hours, and the end product value is drastically diminished with time.
How a Loadout System Works
A loadout system normally consists of two separate screw conveyor systems to keep the offal and feathers separated throughout the process for shipping to the rendering facility. Rotary screens dewater the offal and feathers prior to discharging the material into the conveyor systems. Inclined screw conveyors move the material to the proper height necessary to feed the truck loading horizontal screw conveyors.
Screw conveyors that load trailers are suspended above the truck bay and have multiple discharge points to evenly load from overhead. Heavy-duty hydraulically operated slide gates that are capable of operating in any type of weather conditions can easily be opened and closed in sequence to optimally load the front, middle, and back of the trailer. Diverter gates are also available to distribute the load or to switch between two trailers in a side by side truck bay.
System Design
A typical loadout system conveys offal and feathers with a material density of 40 to 50 pounds per cubic foot and a moisture content of 70 percent to 80 percent liquids. Design capacities average 27,000 pounds per hour, 24 hours per day, seven days per week.<
Due to the wet and corrosive nature of offal and feathers, optimizing design characteristics can have a major impact on preventing maintenance issues and unscheduled downtime. All external screw conveyor parts (troughs, covers, end plates) should be constructed with 304 stainless steel to eliminate corrosion and to facilitate easy washdown.
Conveyor screws must be manufactured with minimum 3/8-inch thick flights continuously welded to a center pipe with extra-heavy wall thickness. Screws should be close coupled and clocked to form a continuous helix that can ride on the trough liners and transport the material efficiently, unobstructed by hanger bearings. Weld-in, abrasion resistant steel (AR-400) trough liners are recommended for long term wear resistance. Hold down angles are typically used to provide an extra level of security for the screws. Because of the wet environment, beltless, motorized drive systems are selected to prevent moisture related, v-belt slippage.
Adding a surge bin to the system allows time for a change of trailers without shutting down the conveyor systems. Upstream processing equipment can continue to operate as the surge bin is loaded with product during the period of time that a full truck pulls out and an empty truck pulls in to be loaded. Once the new trailer is in place, the loadout system restarts, and loading resumes. Eliminating system downtime during the truck loading transition provides additional efficiencies that will pay off on the bottom line.
To block leakage at the lower end of the inclined screw conveyors, the screw pipe is bushed with a bronze sleeve that rotates around a stationary shaft that is bolted to the trough end, thus creating an impenetrable seal. The “dead-end” shaft (Image 4) eliminates leak paths, bearing contamination, premature failure, safety issues, and with routine maintenance, increases the life of the system.
Maintenance
Proper preventive maintenance must be performed to keep screw conveyor loadout systems operating at an optimum level. Checking lubricant levels in reducers at least once a month, along with inspecting for evidence of leaks and bearing wear, are critical to extending the life of the system. If any belt drives are used, routinely examining belts and sheaves for excessive wear is a necessity. End bearings require inspection at consistent intervals. Check screws for wear, straightness and alignment every two months. If the outside diameter of the screw has worn more than one inch, the screws need to be replaced.
Troughs and liners should be checked for excessive wear, misalignment, and leaks every other month. If the liners have worn 50 percent or more, immediate replacement is crucial. With regular preventive maintenance, a properly designed screw conveyer loadout system will operate many years with very little unscheduled downtime.
Sustainability Impact
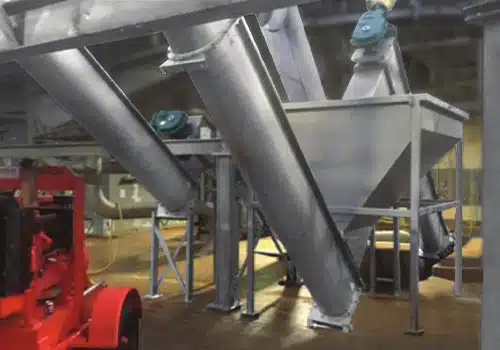
Surge bins allow time for a change of offal trailers without shutting down the offal conveyor system
Rendered products are a big part of the circle of life in the poultry processing business. Without rendering options, byproducts from meat processing would saturate every landfill in the United States in less than four years. Providing a high-protein food choice for animals is a side benefit to the recycling efforts promoted by rendering.
Having an effective and efficient screw conveyor loadout system at the beginning of this process is key to the sustainability of processing over 50 billion pounds of poultry for human consumption, annually.
A well-designed system can withstand anytype of upset conditionand increase process effectiveness, and helpmake preventive maintenance that much easierto extend operation life. Engage your engineeringand operation teams, and/or a third-party specialistto ensure your loadoutsystems are maximizingtheir effectiveness; notonly to the benefit of yourplant, but for your community and beyond.
Jim Collins is executive vice president of KWS Manufacturing. Keith Sandlin is industry segment manager–food and beverage, corporate accounts with MotionIndustries. For more information, visit www.MotionIndustries.com/PoultryTimes. Or view the KWS Behind the Brands You Count On video at https://tinyurl.com/y8qbz3ka.
For more information, please call KWS at 800-543-6558 or visit www.kwsmfg.com.
About KWS: Founded in 1972, KWS Manufacturing Company, Ltd. designs and manufactures conveying equipment for the bulk material handling industry. KWS has a complete product line of mechanical conveying and processing equipment with expertise in providing the correct solution for the application. KWS corporate office and manufacturing facilities are in Burleson, Texas. For more information, please call KWS at 800-543-6558 or visit www.kwsmfg.com.