Vertical Hoppers with Agitators for Fumed Silica
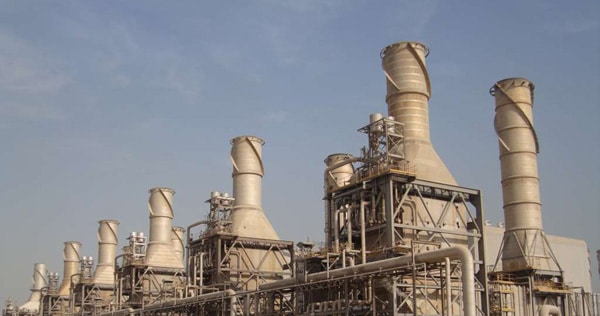
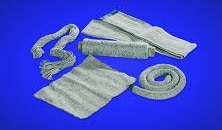
Morgan Thermal Ceramics
Elkhart, IN
General Description
Morgan Advanced Materials is a global materials technology company that offers engineered solutions to several markets. Morgan Thermal Ceramics is a division of Morgan Advanced Materials that is one of the world leaders in heat management technology. Morgan Thermal Ceramics contacted KWS in an effort to locate a manufacturer that could provide a solution to a unique bulk materials processing problem. Hoppers were needed for short-term storage of fumed silica after being conveyed pneumatically from the outdoor storage silos. It was particularly critical that the fumed silica not become stagnant once it was discharged from the pneumatic line into the hoppers. KWS designed and provided hoppers with rotating vertical agitators inside to prevent the fumed silica from becoming compressed and packing while being stored.
Design Parameters
- Product Type: Fumed Silica
- Material Density: 10-20 Lbs. per Cubic Foot
- Storage Capacity: 35 cubic feet (36-Inch Diameter Hopper)

KWS Advantages
The KWS engineering and design team understood the expectations of Morgan Thermal Ceramics and how vertical agitators would work for the specific process. The ideal solution for the application was not readily available and had to be custom-designed. With extensive engineering expertise and experience, KWS was able to start with a blank slate, develop a conceptual design and share the design with Morgan Thermal Ceramics. The cooperation of the two engineering groups allowed the integration of components, such as bin vents and lump breakers from other manufacturers to be flawlessly incorporated into the hopper design. The design was finalized to meet the exact requirements of Morgan Thermal Ceramics.
Special Features
Reduction of downtime and maintenance were very important factors in the design of the short-term storage hoppers. In an effort to increase wear resistance and life expectancy, KWS fabricated the paddles of the vertical agitators from abrasion resistant steel with bolt-on attachments. The bolt-on paddle design allowed for easy replacement to aid in reduced maintenance downtime. The bolt-on, adjustable paddles also offered the operators at Morgan Thermal Ceramics the ability for the paddle pitch, angle of attack, or linear position to be changed for better control of the agitation process.
KWS designed and manufactured two hopper sizes for Morgan Thermal Ceramics based on process needs. A 90-cubic foot hopper with vertical agitator discharged fumed silica directly to a pneumatic conveying line for further processing. The structural supports were simple vertical legs to the floor. A 35-cubic foot hopper with vertical agitator discharged fumed silica onto a rotating turntable directly beneath the hopper discharge. For this reason, a typical four-legged support structure, as used on the 90-cubic foot hopper, could not be utilized to support the smaller hopper. To eliminate any possible issue with instability, KWS designed and built a heavy-duty cantilevered support stand to sufficiently support the load requirements of the 35-cubic foot hopper.
Testimonial
"I have no complaints and no reason to not give KWS a score of 10 out of 10! I would buy from KWS again."
Jorge Martinez, Engineering Manager – Morgan Thermal Ceramics (2014)