Design-Build System Utilizing Live Bottom Screw Feeders, Vertical Screw Conveyor & Hoppers Nuway Tobacco in South Windsor, CT
Nuway Tobacco
South Windsor, CT
General Description
The J.E. Shepard Companies have been an institution in New England since 1888, employing hundreds of people in the fields of manufacturing, consumer products, entertainment and real estate. One of their subsidiaries, Nuway Tobacco, produces high quality wrapping and paper for the manufacturing of cigars. The wrapping is made from tobacco that is shredded, mixed, dried and rolled using a proprietary process. Nuway needed to upgrade their upfront process where tobacco chunks and fines are loaded from the raw product stage and then metered and conveyed to a roller mill. Older, poorly-designed belt conveyors and screw conveyors had become maintenance headaches and leaked too much dust into the building. KWS and Nuway Tobacco worked together to create a heavy duty, custom engineered bulk material handling solution designed from the ground-up.
Design Parameters
- Product Type: Various Sizes of Shredded and Un-Shredded Tobacco Leaves
- Material Density: 5 to 15 Lbs. per Cubic Foot
- System Capacity: 300 Cubic Feet per Hour
- System Duty: 24 Hours per Day, 7 Days per Week
KWS Advantages
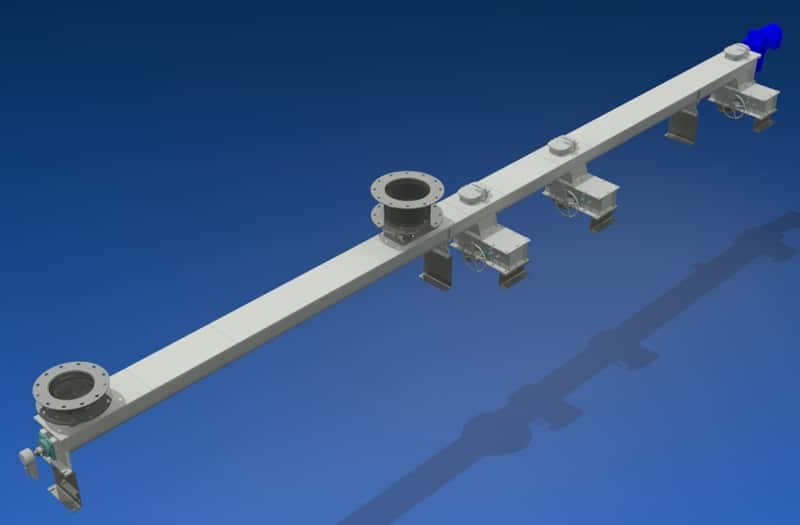
Nuway Tobacco contacted KWS after talking with numerous other conveyor companies without luck; none of the other conveyor companies had the engineering and manufacturing capabilities to match KWS. KWS has 10 degreed mechanical engineers and 4 professional engineers on staff, making KWS a perfect fit for a complex system project. A KWS engineer visited Nuway Tobacco several times to understand their needs on the project. Over the course of several design iterations and in-person drawing reviews, design variables such as capacity, space constraints, maintenance concerns, installation order, mating equipment, controls and safety were incorporated into the solution. The KWS engineering team created the full system layout in Autodesk 3D Inventor with plenty of detail to bring the design to life. KWS worked hand-in-hand with Nuway Tobacco to provide the equipment in the proper order so it could be installed in sequence.
Special Features
KWS designed a special live bottom hopper with a unique bridge breaker and screw feeder to meter the raw product into a vertical screw conveyor. The hopper needed to fit in a tight space while the screw feeder metered the raw product up an incline of 20 degrees, providing the capacity needed. A dust-tight vertical screw conveyor replaced the old, leaky equipment to get product up to a hammer mill. In a separate part of the process, KWS also engineered a hopper with a screw feeder and screw conveyors for transferring dust from the collection system to a roller mill. KWS also designed the chutes, supports, and hoppers from the vertical screw conveyor to the shredding and separation process. KWS engineers designed in the mating structure for the necessary level indication switches, access panels, magnets, airlocks, and explosion suppression ports in each piece of equipment. The KWS system is much heavier duty, cleaner, and safer to the operator than the previous solution.
Testimonial
"This project had a complex path from start to finish as my plant’s needs evolved. Once the design was locked in, all the equipment was built quickly and worked perfectly. I couldn’t be happier with how our partnership with KWS turned out."
Rick Gendreau, Engineering Manager – Nuway Tobacco
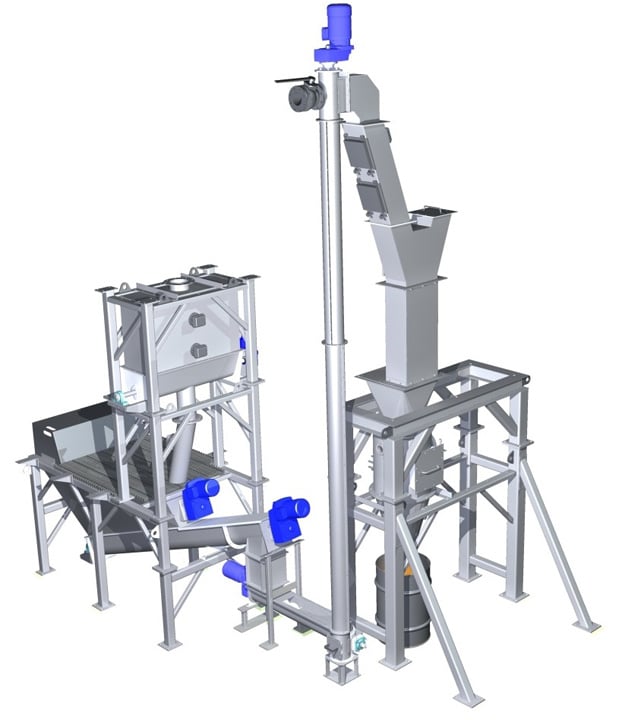
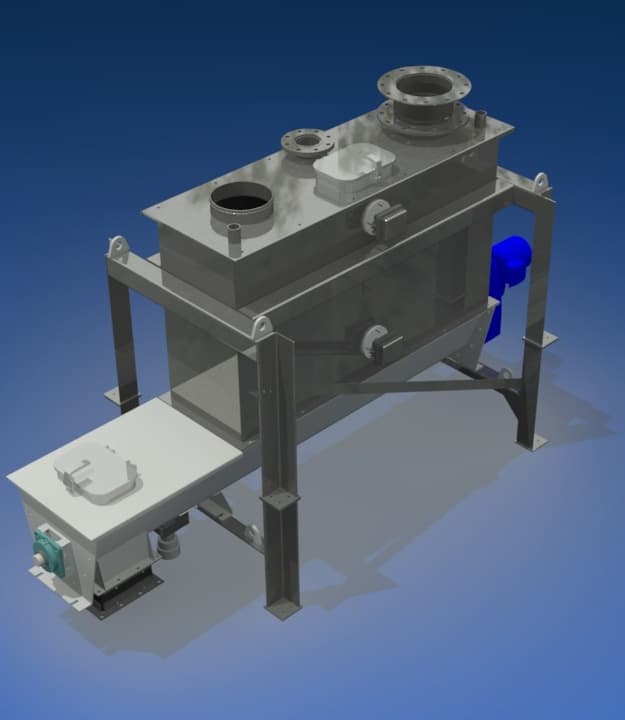