Triple-Screw Mass Flow Screw Feeder and Injection Screw Conveyor For Alternative Energy Producer
General Description
Approximately 15-percent of the solid waste in the US is processed and converted into alternative energy, equivalent to almost 30 billion barrels of crude oil. The EPA estimates that energy recovery systems help prevent the release of over 40 million tons of carbon dioxide annually. Waste plastics have a high energy value and are a key feedstock for energy recovery technologies.
An alternative energy producer is at the forefront of the development of a revolutionary pyrolysis process. The ultimate goal is to prevent plastic from reaching a landfill or incinerator. Over many years of development, the company has gained global recognition for developing a very efficient pyrolysis process.
As part of an expansion at the facility, the alternative energy producer and KWS created a working partnership to design and implement a new raw material feed system for the pyrolysis reactor. KWS provided a mass-flow live bottom screw feeder to ensure accurate and reliable metering of various shredded and pelletized plastics. KWS also provided a cantilevered injection screw conveyor to receive the material from the mass-flow feeder and discharge it directly into the pyrolysis reactor. KWS also supplied a feed hopper with a reverse taper to prevent the plastic materials from compacting while being loaded and stored.
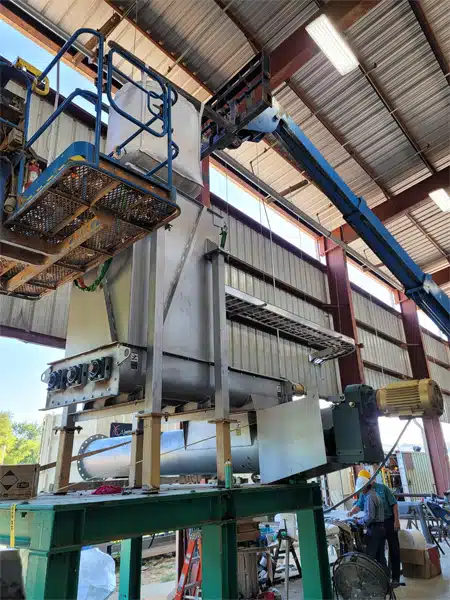
Waste Plastic is Stored and Metered Accurately
Design Parameters
- Product Type: Shredded & Pelletized Plastic
- Material Density: 2 to 8 Lbs. per Cubic Foot
- Conveyor System Capacity: 2,000 Cubic feet per Hour
- Duty: Intermittent
KWS Advantages
Engineers from KWS made several site visits during the initial design phase to collaborate with engineers at the company and their partner companies to ensure the ideal solution was being offered to meet their unique application needs. Waste plastic is very light, with irregular shapes that cause a multitude of problems for storage, metering and conveying. KWS has extensive experience with waste plastics and proper design of material handling equipment.
KWS Special Features
KWS designed and manufactured a surge hopper with negatively sloping walls to prevent material bridging and a mass-flow live bottom screw feeder to accurately meter the various shredded plastics from the hopper. The term “mass flow” describes a material flow pattern in which all material in the hopper is drawn down at the same rate, regardless of if the material is against the sidewall or in the center. This feature allows the material to be drawn down evenly along the entire length of the inlet opening of the live bottom screw feeder. Accurate feed rate is extremely important for a successful process.
The new KWS injection screw conveyor receives material from the live bottom screw feeder and is directly bolted to the inlet flange of the pyrolysis reactor. The discharge end of the injection screw conveyor is exposed to temperatures in excess of 500-degrees F. KWS designed the conveyor to be cantilevered and supported on only on the drive end. The cantilevered design eliminates any potential maintenance issues and downtime associated with a shaft seal and bearing in the high-temperature zone.
The cantilevered screw is supported by a double pillow block bearing arrangement with a torque arm drive unit. The torque arm configuration allows the shaft mounted gear reducer to “float” on the drive shaft and any binding resulting from misalignment or cantilevered screw deflection is eliminated.
Testimonial
"We are extremely pleased with KWS and the installation of the plastics feed system. We are looking forward to our continued partnership with KWS as we complete our expansion."
Plant Manager – Alternative Energy Producer
Waste Plastic is Very Light with Irregular Shapes
Cantilevered Screw Injects Waste Plastic into Reactor
Waste Plastic Varies in Size and Density
Waste Plastic Have High Energy Value and Feedstock for Energy Recovery Systems
End View of Cantilevered Screw
Video of Injection Screw Conveyor Test Run