Shaftless Screw Conveyors for Loading Biosolids to Dumpsters Pataskala WRF in Pataskala, OH
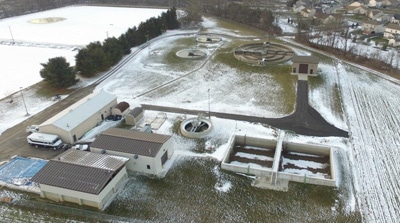
The City of Pataskala Utility Department
Pataskala, OH 43062
W.E. Stilson Consulting Group
Columbus, OH 43235
Kirk Bros. Co., Inc. - General Contracting
Pataskala, OH 43062
Pataskala WRF
Pataskala, OH 43062
General Description
All of the wastewater in Pataskala, OH is delivered to the Pataskala Water Reclamation Facility (WRF) through a 34.5 mile network of pipelines where it is treated and ultimately released to the south fork of the Licking River. As part of their solids handling system, Pataskala WRF required a means to transfer dewatered biosolids from an existing dewatering building to a new loading building. The city recognized the benefits of using shaftless screw conveyors to transfer the biosolids from rotary presses to the truck loading area to distribute the biosolids into dumpsters and trucks. The system was automated to limit operator involvement and speed up truck loading, both of which saved the city money.
KWS Environmental designed and manufactured the biosolids transfer and loading system which included shaftless screw conveyors, transitions from the rotary presses and controls. Since the transfer screw conveyor had to move material between buildings and was exposed to outdoor climate, it was equipped with heat tracing.
Design Parameters
- Type of Sludge Municipal Dewatered Biosolids
- Material Density – max: 60 to 65 Lbs. per Cubic Foot
- Solids, percent by weight: 20 to 24-percent
- Capacity (max): 6.75 to 13.50 Wet Tons per Hour
- Capacity (max): 210 to 420 Cubic Feet per Hour
- Duty: 24 Hours per Day, 7 Days per Week
KWS Advantages
KWS Environmental designed the shaftless screw conveyor system to fit within the space constraints of the dewatering building. The system was designed so that the horizontal shaftless screw conveyor fit in the limited space beneath the rotary presses and discharged vertically to the inclined shaftless screw conveyor. The drive unit on the inclined shaftless screw conveyor was located near the ceiling of the loading area with very little clearance. KWS Environmental supported the drive unit from the ceiling to eliminate a floor support and provide more room to load dumpsters and trucks. Heat tracing was provided on the area of the inclined conveyor that was exposed to winter weather to prevent the biosolids from freezing and causing issues.
Special Features
KWS Environmental provided a complete biosolids load out system including shaftless screw conveyors, supports and control panel. The shaftless screw conveyors utilized the KWS-350 Ultra Strong Micro-Alloy spirals for long life along with two-color Wear Alert liners. The two-color liner provides a visual indicator that the liner life has expired. When the top layer is worn through, a second highly contrasting color layer becomes visible and indicates that the liner must be replaced. Measuring liner thickness on equipment that is in service is difficult and this is a very useful feature for plant operators. The self-contained, stand-alone control panel provided a completely automated load out system including controls for the heat tracing.
Testimonial
"The load out system provided by KWS Environmental works perfectly. Thanks for all your help!"
Tim Essinger – Project Manager, Kirk Brothers