Shaftless Loadout Conveyor for Dewatered Biosolids for Webb City, MO
City of Webb City
Webb City, MO
Allgeier, Martin and Associates, Inc.
Joplin, MO
G&G Construction
Carthage, MO
Center Creek WWTP
Webb City, MO
General Description
Webb City is in southwestern Missouri with a wastewater collection system that consists of a total of 63 miles of pipe and 9 lift stations. The plant is permitted for a design wastewater rate of 5 million gallons per day (MGD). As part of a plant upgrade, new screening and sludge dewatering equipment were added to produce high-quality biosolids from the wastewater stream. The addition of a new centrifuge for sludge dewatering required a new KWS Environmental shaftless screw conveyor to transfer the biosolids to an outdoor truck loadout area.
Design Parameters
- Product Type: Dewatered Biosolids
- Material Density: 50 Lbs. per Cubic Foot
- Max Capacity: 160 Cubic Feet per Hour
- Duty: 5 days a week, 8 Hours per Day
KWS Advantages
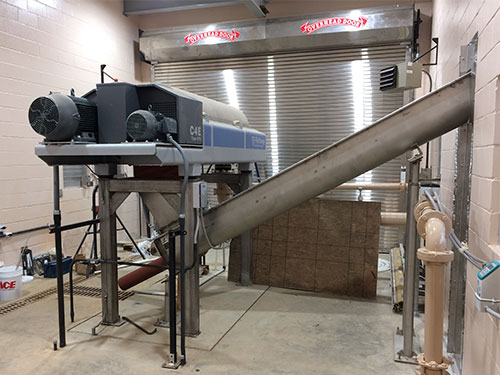
Centrifuge Discharges Dewatered Biosolids to KWS Shaftless Screw Conveyor
KWS Environmental has provided several successful projects to G&G Construction and the consulting engineer and was an easy fit for the Webb City project. KWS provided a high quality and high value package that included the centrifuge and loadout conveyor. KWS team has over 1,000 successful installations with proper interface to centrifuges and other process equipment. The equipment shipped ahead of schedule and installed cleanly. A degreed mechanical engineer from KWS provided a customized startup procedure, O&M manuals, and on-site training to ensure the equipment was put into service correctly.
Special Features
KWS selected a shaftless screw conveyor to convey and elevate sticky and wet biosolids. A drain was located at the lower end so the conveyor could be run in reverse and low-percentage biosolids diverted while the centrifuge is ramping up.
The conveyor trough and covers were constructed from 304 stainless steel to provide corrosion protection. KWS engineered a custom inlet chute to interface to the centrifuge outlet and transition to the conveyor. A zero-speed switch was added to shut down the conveyor when a loss of screw rotation is detected. KWS also provided an emergency stop switch to immediately shut down the conveyor if an adverse running condition is noticed. Both the zero-speed and emergency stop switches help keep plant personnel safe along with protecting the loadout system from damage.
Testimonial
"The conveyor and associated parts went together well and there were no problems during installation or startup."
Dennis Johnson – Project Manager, G & G Construction Co., Inc.
Special Inlet Transition Chute Fits Perfectly to Centrifuge
Large Diameter Drain Diverts Low Solids Back to Process
Stainless Steel Structural Supports for KWS Conveyor
Biosolids are Discharged to Trucks or Containers
Truck Being Loaded with Biosolids for Disposal
Zero Speed Switch Detects Loss of Rotational Speed of Shaftless Spiral
Switch is Activated by Pulling Cord to Remove Power to Conveyor