Screw Feeders and Conveyors for Handling Electric Arc Furnace Dust American Zinc Recycling in Rockwood, TN
General Description
Making steel in electric arc furnaces produces electric arc furnace (EAF) dust, a hazardous waste byproduct that steel manufacturers have typically captured and stored in landfills. EAF dust contains non-ferrous metals such as zinc, iron and nickel, which are valuable recyclables.
American Zinc Recycling (AZR) receives EAF dust from steel manufacturers and with a multi-step process, separates valuable zinc metal to be reused as feedstock for zinc metal production. As part of the separation process, EAF dust is mixed with coke and heated in a kiln. AZR needed to expand and improve their process flow in a very short time period due to increased demand. KWS was contacted by AZR due to past successful projects together and KWS’ extensive knowledge of conveying EAF dust. AZR knew KWS was the only conveyor manufacturer that could provide a complete engineered solution within a few weeks.
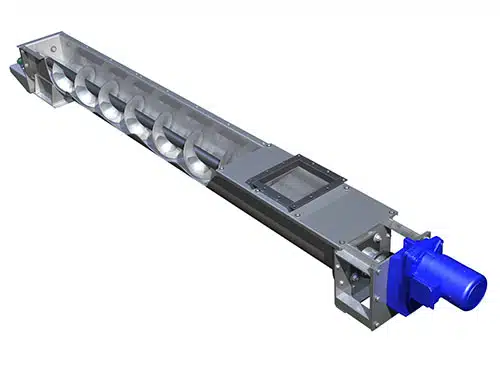
KWS Provided Heavy-Duty Screw Conveyors for Conveying Abrasive EAF Dust
Design Parameters
- Product Type: Electric Arc Furnace Dust and Filter Cake Mixture
- Material Density: 47 to 110 Lbs. per Cubic Foot
- Capacity: 490 Cubic Feet per Hour
- Duty: 24 Hours per Day, 7 Days per Week
KWS Advantages
KWS engineers provided AZR with quick reference 3D models and drawings during the quoting stage to help reduce lead time and ensure the layout would work in the new area of the plant. Since AZR was building a new expansion to their plant, the layout went through several design iterations over the span of a week with KWS working closely to provide a modular solution. Once the design was finalized, KWS immediately began production. Normal lead time was 12 weeks, however KWS manufactured and delivered the complete project in less than 5 weeks, eliminating any project delays.
Special Features
AZR built new storage hoppers for both EAF dust and filter cake. KWS screw feeders metered the bulk materials from the individual hoppers to transfer screw conveyors. Each bulk material was then discharged to a common batch mixer. After mixing, KWS screw conveyors transferred the mixture to a secondary storage bin. KWS also supplied another screw feeder to meter the mixture to a kiln to start the recycling process. KWS utilized heavy-duty CEMA standard components that are modular in design and built for the abrasive nature of the application. Abrasion resistant AR400 screw flights were used to handle the EAF dust to increase the life span of the system.
Testimonial
"I appreciate the quick response and incredibly fast delivery of the KWS screw conveyor systems. These conveyors were originally our timeline bottleneck until KWS stepped up and provided a quick, high quality solution."
Jeff Rihn, Project Manager – American Zinc Recycling
Each KWS Screw Section Utilized AR400 Abrasion Resistant Material
Hard Iron Bearings with Hardened Shafts are Designed for Trouble-Free Operation
All Screws were Continuously Welded on Both Sides for Added Strength