Screw Conveyor for Conveying Activated Carbon at 1,800-Degrees F
General Description
Activated carbon is a highly porous media that attracts and absorbs organic chemicals. The media is created by pyrolyzing a carbonaceous substance, such as nutshells, coal, wood, or peat without oxygen to make carbon char. The char is treated to develop an interconnected series of pores inside the carbon. The great surface area of this internal pore network results in an extremely large surface area ideal for adsorption and holding organic chemicals.
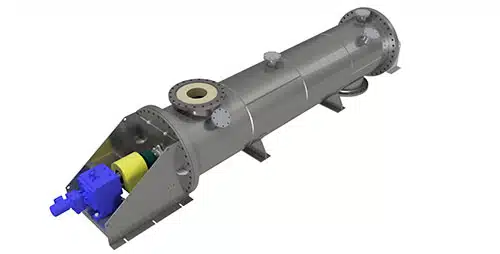
KWS Screw Conveyor Handles Activated Carbon at 1,800-Degrees F
Specially-Designed Trough End Allows for 4-Inches of Axial Thermal Expansion
A major activated carbon producer developed an innovative process to create its product more effectively and efficiently than traditional kiln and oven methods. The proprietary process produces activated carbon at a lower cost while maintain high quality. KWS and the activated carbon producer collaborated to design a screw conveyor capable of conveying material at 1,800-degrees F while limiting heat loss. It was also critical that the material remain in the screw conveyor for a designated residence time during the continuous process.
Design Parameters
- Product Type: Activated Carbon
- Material Density: 25 to 35 Lbs. per Cubic Foot
- Conveyor System Capacity: 80 Cubic Feet per Hour
- Temperature: 1,800-degrees F
- Pressure: 1 psig
- Duty: Continuous
KWS Advantages
Engineers at KWS were able to determine the size and length of the conveyor not only based on this customer’s required throughput capacity but also the necessary residence time. Engineers were able to combine the use of a large diameter screw, reduced pitch, and very low-speed drive to design the ideal solution. KWS provided thermal structural analysis of the conveyor at 1,800-degrees F to ensure no issues would result from the circumferential and axial thermal expansion of the internal components.
KWS Special Features
Inside of Vessel is Lined with 5-1/2-Inches of Refractory
To maintain temperature and eliminate heat loss, KWS lined the interior of the vessel walls with refractory lining. KWS fabricated the heavy-duty 304 stainless steel vessel shell and worked with the experts at Morgan Thermal Ceramics to install the Koa-Tuff lining. This lining was selected based on excellent insulating properties as well as resistance to abrasion and erosion at elevated temperatures. The refractory measures 5-1/2-inches thick around the screw and 3-inches thick on the trough ends for optimal heat containment.
KWS designed and manufactured a slider-base pedestal trough end to protect the tail bearing from contamination and allow for thermal expansion. Expansion and contraction are common in every high-temperature application and occur axially along the length of the screw and trough. The KWS slider base trough end is designed for thermal expansion and can account for axial expansion up to 4 inches.
The unit was designed with a single-piece 310 stainless steel screw to withstand high temperature with minimal deformation. The screw was designed to span the entire conveyor length without the use of an intermediate support/hanger bearing. The large diameter center pipe of the screw was oversized to minimize screw deflection. KWS engineers adjusted the torque rating of the center pipe and power transmission components to account for the elevated temperature exposure.
Testimonial
"We are very happy with the KWS product. It is working very well. We look forward to working with KWS on our next generation plants and other projects."
Chairman – Major Activated Carbon producer
High Temperature Screw Conveyor Installed and Operating
Activated Carbon is Retained in Vessel for Several Minutes at 1,800-Degrees F
Refractory Lining has Excellent Heat Retention Properties