Mass Flow Screw Feeder for EAF Filter Dust
General Description
Steel mills in the United States primarily utilize electric arc furnaces in production. One of the by-products of this process is electric arc furnace dust (EAF), which contains zinc and other heavy metal elements. EAF dust is transported to a recycling facility where it is processed to recover the zinc.
In order to maintain a regular flow rate for the plant, material is metered out of large storage silos via screw feeders. Due to repeated occurrences of product bridging and ratholing, the Customer sought to replace the silo and screw feeder with a mass flow design. Mass flow screw feeders employ a cone and variable pitch to evenly draw material from the full length of a hopper or silo, thereby eliminating problems which arise from product solidifying in the hopper.
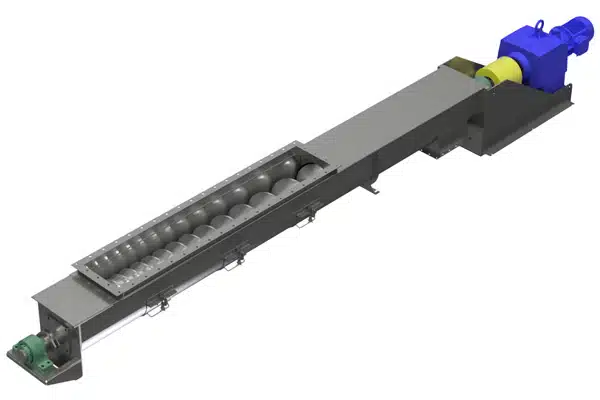
Mass Flow Screw Feeder Meters Electric Arc Furnace Dust
Design Parameters
- Product Type: Electric Arc Furnace Dust (EAF)
- Material Density: 70 to 100 Lbs. per Cubic Foot
- Capacity: 486 Cubic Feet per Hour
- Duty: 24 Hours per Day, 7 Days per Week
KWS Advantages
After dealing with problems for over a year after installation, the Customer sought to redesign the storage silo and screw feeder. With over 50 years of experience in providing the highest quality solutions in the bulk material handling industry, KWS was brought in to replace the screw feeder. The Customer’s bottom line relies on efficiently recycling EAF dust without having to manually unload portions of their storage silos. KWS provided a robust mass flow screw feeder capable of evenly drawing material along the full length of the long rectangular inlet.
KWS Special Features
EAF dust is very dense and abrasive. Working with Jenike & Johanson, KWS provided a mass flow screw feeder capable of handling the most extreme conditions. The mass flow screw utilizes a heavy-wall cone section, with internal support gussets, extending through half of the inlet area and followed by variable pitch flights. Every pitch of the screw has an increasing volumetric capacity, pulling more material along the length of the inlet. The screw flights themselves are further protected by an overlay of hardsurfacing along the carrying face and periphery.
Welded flange trough ends provide a tight seal with heavy-duty bolted covers, eliminating potential paths for dust leakage. Pedestal trough ends also allow for additional clearance between the conveyor housing and support bearings, thereby extending bearing life by decreasing opportunities for material to contaminate them. Flanged gland seals with multiple rings of rope packing to retain material within the feeder housing. KWS utilized and in-line drive unit to start the screw feeder under a 40-foot tall head load.
Testimonial
"KWS provided an excellent piece of equipment, very heavy-duty and designed to eliminate repetitive problems we’ve dealt with since the previous silo and feeder were installed."
Plant Manager – Zinc Recycling Company
Exploded View of Drive End with In-Line High Torque Drive Unit
EAF Dust is Drawn Evenly from Silo Along Length of Rectangular Inlet
Mass Flow Screw Utilizes Cone and Variable Pitch Flighting
Pedestal Trough End with Flanged Gland Seal Protect Bearings and Contain EAF Dust