Loadout System for Offal and Feathers Pilgrim's Chicken Processing Plant in Lufkin, Texas
General Description
For over sixty years, Pilgrim’s has produced healthy, high-quality food products for consumers all over the world. Pilgrim’s is currently the second-largest chicken producer in the world and has the capacity to process more than 34 million birds per week for a total of more than over 10 billion pounds of live chicken annually.
The Pilgrim’s chicken processing plant in Lufkin, TX processes 250,000 chickens each day. No part of a chicken is wasted. Once the edible portions have been separated, the remaining portions are offal and feathers. Offal refers to the internal organs and entrails of a butchered animal. Offal is processed at the offsite rendering plant, producing material that is used for fertilizer, fuel or as protein meal that is used as an additive for pet food. The offal category includes certain chicken organs, as well as any other portion of the chicken not used. These categories are kept segregated throughout the process and shipped separately to the rendering facility. Feathers are processed into feather meal and are a very high density source of protein for animal feed.
Design Parameters
- Product Type – Offal and Feathers
- Material Density – 40 to 50 Lbs. per Cubic Foot
- Conveyor System Capacity – 27,000 Lbs. per Hour
- Moisture Content: – 70 to 80-Percent Liquids
- Duty – 24 Hours per Day, 7 Days per Week
KWS Advantages
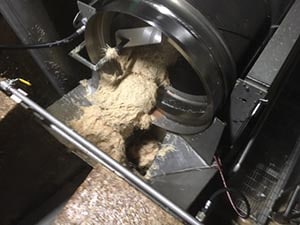
Feathers are dewatered in rotary screen and discharge to KWS screw conveyor.
The existing offal and feather loadout systems at the Pilgrim’s plant in Lufkin was in serious need of an upgrade. Constant problems with both loadout systems were causing interrupting plant operations and affecting profitability. Pilgrim’s needed a better, more reliable system for loading offal and feathers.
A team from KWS, led by the KWS Ag By-Product Manager, with over 38 years’ industry experience, and KWS Design Engineers visited the Lufkin facility and met with the Pilgrim’s Plant Manager to identify the problems and offer long-term, cost-effective solutions. The project was on a very short time line and had to go from concept to completion in less than six weeks. Pilgrim’s knew KWS was the only screw conveyor manufacturer in the US that could meet their demands. KWS was up for the challenge.
Special Features
Offal is dewatered in rotary screen and discharges to KWS screw conveyor.
The existing offal screw conveyors utilized UHMW trough liners that would “pop out” and shut down the complete loadout system, creating a maintenance nightmare. The new KWS loadout systems utilized weld-in abrasion resistant steel AR-400 trough liners that would last many years and could not “pop out”. The new KWS conveyor screws were manufactured with 3/8-inch thick flights that were continuously welded on both sides of a center pipe with extra-heavy wall thickness. These screws could withstand any type of upset condition and last the life of the loadout system.
Leakage of liquid was another big issue at the plant. The existing inclined screw conveyors leaked at lower end, causing more maintenance and safety problems. The new KWS inclined screw conveyors utilized the exclusive KWS Dead End Shaft design to eliminate liquid leakage at the lower end and also eliminate bearing contamination and failure.
By working with Pilgrim’s to understand the sequence of operations for the loadout system, KWS added a surge bin to the system to allow time for a change of offal trailers without shutting down the offal conveyor system. The upstream processing equipment could continue to operate continuously as the surge bin was loaded with product while a trailer was changed out. Once a new trailer was in place, the loadout system would restart, and loadout would resume.
The existing loadout system was very rusty and corroded due to the wet and corrosive nature of the offal and feathers. The new KWS loadout screw conveyors were constructed from 304 stainless steel on all external parts (troughs, covers, end plates). With 304 stainless steel construction, corrosion was eliminated and equipment wash down made easy. The wet conditions at the plant also caused belt slippage on the existing screw conveyor drives, creating another maintenance headache. KWS eliminated belt drives completely by using Dodge Motorized Torque Arm (MTA) C-face reducers.
The pneumatic lines to operate the existing slide gates would freeze in cold weather preventing the slide gates from operating, again causing an interruption of the loadout operations. KWS designed and manufactured heavy-duty hydraulically operated slide gates that would operate in any type of weather conditions, even in freezing weather.
KWS and Motion Industries fully understood Pilgrim’s project requirements and the very tight timeline. Utilizing the combined resources of Motion Industries and KWS, the conveyors were designed, manufactured and delivered one week ahead of schedule. Motion Industries provided key engineering and dimensional information to KWS from the site in Lufkin, Texas and also supplied all of the power transmission components such as the Dodge Motorized Torque Arm (MTA) C-face reducers, bearings and hydraulic cylinders to KWS. The Lufkin project was a huge success and a new project in Nacogdoches, Texas is currently in process.
Testimonial
"Nice project! KWS worked very closely with Motion Industries as well as the consulting engineers and contractor to ensure drawing accuracy and fit up in the field. KWS expedited the approval process and handled several design revisions. We appreciate your knowledge of the process and solutions to the existing problems in the loadout area. The KWS quality was excellent! The equipment was delivered one week prior to the required date. We are ready to move on to the next project!"
Joshua Watson, Account Representative – Motion Industries
KWS surge bin allows time for a change of offal trailers without shutting down the offal conveyor system.
KWS inclined screw conveyors transfer feathers and offal to truck load screw conveyors.
KWS hydraulically operated slide gates are designed to operate under harsh conditions.
KWS load out screw conveyors evenly load trailers with offal and feathers.