Inclined Screw Conveyor for Conveying Talc to Pneumatic Conveying System
LyondellBasell (Equistar Chemicals) Mansfield, TX
General Description
LyondellBasell (LYB) is one of the world’s largest chemical producers. Its subsidiary, Equistar Chemicals produces polymer products including polyolefin resins and polyethylene. As part of an upgrade of an existing product line, Equistar required a new Loss-in-Weight volumetric feeder and a collection screw conveyor. Talc is metered by the volumetric feeder to an inclined screw conveyor which then discharges to a pneumatic conveying system. The screw conveyor is used to smooth the variations from the upstream feeder and limit surging into the pneumatic conveying line. The process results in materials that can be used to manufacture countless consumer and industrial goods.
As part of the planned upgrade, it was imperative that LYB improve the performance of the existing screw conveyor which had become very problematic over the years. KWS evaluated the current design of the screw conveyor, provided a diagnosis, and offered an enhanced design that would eliminate all their performance concerns.
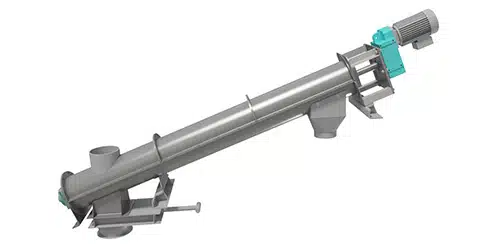
Inclined Screw Conveyor Discharges Talc to Pneumatic Conveying System
Design Parameters
- Product Type: Talc
- Material Density: 20 to 30 Lbs. per Cubic Foot
- Conveyor System Capacity: 210 Cubic Feet per Hour
- Duty: Intermittent
KWS Advantages
KWS and LYB engineering teams collaborated to ensure a successful project. To assist LYB through the preliminary phase of the project, KWS provided engineering services to generate a 3D parametric model of our proposed solution. This allowed the LYB team to input the new conveyor into a 3D scan of the plant guaranteeing the new screw conveyor would fit into the existing space constraints.
KWS Special Features
Double Flights Smooth Discharge and Eliminate Surging
LYB expressed concerns about talc leaking through the shaft penetrations of the existing unit. KWS solved the leaking problems by utilized self-adjusting, air purged CinchSeals. CinchSeals use an elastomer that is molded slightly smaller than the shaft size creating an interference fit. Rotating rotor cups compress against two stationary stator plates to create the primary seal to stop bulk material leakage. The seals are air purged at 5 to 7-PSI above internal screw conveyor pressure to maintain a positive seal.
To rid the system of any bulk material that does not meet the customer’s specifications, the screw conveyor was fitted with a bypass discharge located directly below the inlet spout. KWS worked with Salina Vortex to incorporate a manual slide gate that could quickly be opened and closed as needed. The rejected material is loaded into a bulk bag for further processing. To accommodate the loading of the bulk bags, KWS also supplied a transition chute with an integral safety screen to protect plant personnel.
Double flights were used at the discharge end of the screw to provide even discharge and eliminate surging. Double flights add a second set of flights mounted 180-degrees apart from the first set of flights. The outside diameter and pitch are equal with double flights, very similar to a standard pitch, single flight screw so there is no reduction in volumetric conveying capacity.
Testimonial
"The conveyor installed and looking good. Thanks for the upfront engineering design work to ensure the equipment installed and performed perfectly."
Jon Donlon, Project & Reliability Engineer – LyondellBasell
Air Purged CinchSeals Maintain a Positive Seal and Eliminate Leakage
Bypass Discharge is Used to Remove Unwanted Bulk Materials from Process