Inclined Screw Conveyor & Bucket Elevator Conveying Copper Powder
General Description
Highly pure copper powder is used in a variety of applications including plating electrical devices, abrasives, bearings and even as a pigment. Copper powder is produced from materials such as scrap copper or processed copper ore. Scrap copper is ground and then processed to remove impurities. Enclosed screw conveyors are important to the process to prevent loss of valuable product due to leaks or spills. A metal powder producer was upgrading a copper powder process and needed a system to transport copper powder vertically from a grinder to a distribution point almost 20 feet in the air. KWS designed an inclined screw conveyor and bucket elevator that exceeded expectations.
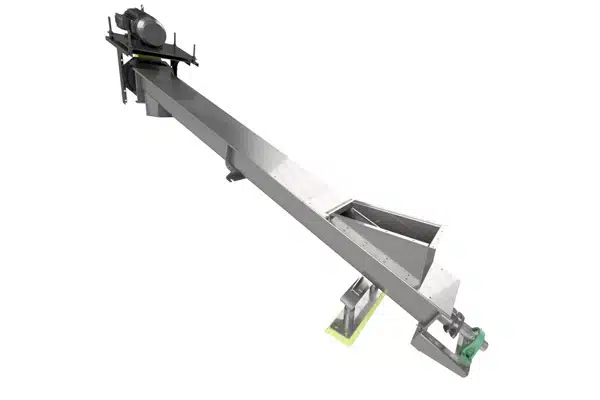
Grinder Bolts Directly to Inlet of Screw Conveyor
Design Parameters
- Product Type: Copper Powder
- Material Density: 225 Lbs. per Cubic Foot
- Capacity: 27 Cubic Feet per Hour
- Duty: 24 Hours per Day, 7 Days per Week
KWS Advantages
In seeking higher productivity, a new copper powder processing line was required. The existing building for the new production line was relatively small, creating issues with conveyor selection and design. Conveying copper powder efficiently required careful collaborative design with engineers from KWS and the end user. A new inclined screw conveyor was required to gather material from the grinder. A bucket elevator was selected to elevate the copper powder to the next phase of the process. With the aid of 3D modeling software, KWS fit the new equipment exactly in the available space and utilized the smallest footprint possible.
KWS Special Features
Both the inclined screw conveyor and bucket elevator were designed and manufactured to convey very dense copper powder. Additional horsepower and torque were needed to convey and elevate the bulk material weighing 225 lbs. per cubic foot. Heavy-duty construction with dust-tight covers ensured there was no leakage of material.
Flanged gland seals mounted on all rotating shafts provided a superior seal, and extended bearing life. The lower end of the screw conveyor was mounted on an adjustable structural support, making installation easy for a perfectly aligned unit. A special inlet chute to the grinder discharge fit up perfectly. To withstand the rigors of 24-hour operation, the robust KWS bucket elevator featured heavy-gauge intermediate sections and included multiple inspection access points for ease of maintenance.
Testimonial
"With such a small footprint to work in, communicating directly with KWS engineers was critical to making this expansion work. By exchanging 3D models, we dialed in exactly what we needed."
Plant Manager – Metal Powder Producer
Copper Powder is Conveyed and Elevated for Processing
Bucket Elevator Easily Elevates Dense Copper Powder