Heavy-Duty, Large Capacity Hoppers and Mass-Flow Screw Feeders to Meter Gypsum and Bottom Ash
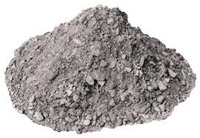
Ghent Generating Station
Ghent, KY
General Description
Located on the Ohio River northeast of Carrollton, Kentucky, the Ghent Generating Station is Kentucky Utilities Company’s largest coal-fired power plant. Ghent is one of the most environmentally sound and technologically advanced coal-fired power plants in the nation while complying with the most stringent federal and state air, water and waste regulations. The station consumes an average of 5.5 million tons of coal annually. Two of the byproducts of coal combustion include gypsum and bottom ash. Bottom ash can be used as a component of concrete blocks and gypsum can be used in plaster or as a soil conditioner. In this process, the reclaimed gypsum and bottom ash is transferred via front end loaders to KWS hoppers with twin mass-flow screw feeders. The screws meter the product onto takeaway belt conveyors that transfer the products to be weighed, separated, and sifted so it can be sold for commercial use. KWS worked together with Beumer, a leading cement and bulk material system supplier, to develop a robust solution for this application.
Design Parameters
- Product Type: Gypsum and Bottom Ash
- Material Density: 75 Lbs. per Cubic Foot
- Capacity: 16,667 Cubic Feet per Hour
- Duty: 24 Hours per Day, 7 Days per Week
KWS Advantages
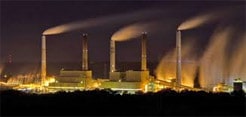
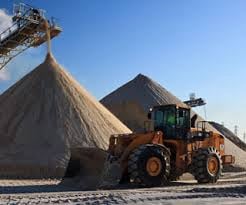
Beumer contacted KWS after viewing the wealth of information on our website. They were looking for a manufacturer with the design knowledge and material handling expertise to provide a solution for the plant’s reclaim process. KWS excels at heavy-duty bulk material applications. Large-scale projects require a very keen sense of detail, which KWS project managers, engineers and designers all have the background and training for. KWS reviewed the project specifications and drawings in great detail to understand the requirements. KWS made improvements by adding a mass-flow design to the screw feeders and upsizing the horsepower and construction of the design to make it extremely heavy-duty. The mass-flow profile of the screw feeder is an ideal design for long inlets because it promotes mass flow and prevents bridging. KWS has many years of experience with designing hoppers and mass-flow screw feeders. The hoppers were designed in 3D with Autodesk Inventor to prevent interferences and to perfectly interface with the front end loaders and downstream equipment.
Special Features
Beumer required a very robust hopper and feeder design that could handle being loaded by front end loaders 24/7. KWS designed 24-inch diameter twin-screw feeders with mass-flow profiles to meter the product and prevent bridging. The 500-cubic foot hoppers were engineered to promote even loading and flow. The hopper structure was designed using heavy-duty I-beams that bolted together for ease of transport and assembly. The screw flights were extra thick to handle the abrasive and corrosive products. The side walls of the troughs and hoppers were designed with extra structural support to withstand the harshest conditions. KWS designed both the inlet and discharge ends with compact shaft seals and gear reducers to save space. KWS provided individual drives on each screw to transmit maximum torque. Each motor was supplied with a heater for operation in icy conditions.
Testimonial
"Thanks for all the support during the project, the KWS feeders are performing well."
Adam Naber, Construction Manager – Beumer Group