Hopper and Screw Feeder for Recycling Plastic Fluff
General Description
Radici Group provides specialty chemicals and high performance polymers to many industries including textiles, automotive, and energy. With production plants located on four continents and sales sites in many countries across the globe, Radici controls their production chain from raw chemicals to custom tailored products.
Previously used plastic components are recycled and shredded into fluff that gets melted and extruded into pellets. Radici has constant focus on the efficiency and quality of production processes, products, and services using recent technologies and innovative systems. Shredded plastic fluff required storage and metering for the pelletization process. KWS has over 50 years in solving difficult bulk material handling problems.
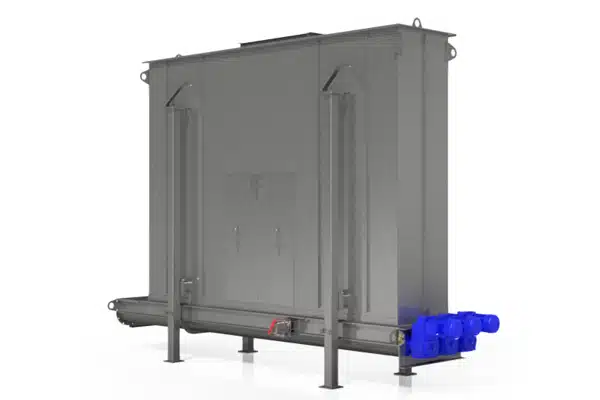
Light Density Plastic Fluff is Stored and Accurately Metered
Design Parameters
- Product Type: Plastic Fluff
- Material Density: 3.25 Lbs. per Cubic Foot
- Capacity: 89 Cubic Feet per Hour
- Duty: 24 Hours per Day, 7 Days per Week
KWS Advantages
KWS and Radici worked together to develop a long-term cost-effective solution for their needs. Storing and metering plastic fluff with a bulk density of only 3.25-lbs. per cubic foot is extremely difficult and requires special design considerations. Low density and fluffy bulk materials tend to bridge in hoppers and are difficult to accurately meter. KWS has provided many successful systems for the plastic recycling industry.
KWS designed and manufactured a hopper with live bottom screw feeder to store and meter the plastic fluff to a weight belt and further processing. KWS used the latest 3D modeling techniques to ensure proper hopper and screw feeder design and made sure the system fit in the available area.
KWS Special Features
Hopper design required the use of vertical walls to prevent compression and bridging of the plastic fluff. KWS also used mass flow design fundamentals for both the hopper and screw feeder. Mass flow screw feeders are the most efficient method to meter bulk materials. The term “mass flow” describes a material flow pattern in which all material in a bin is drawn down at the same rate. Mass flow screws utilize a unique design to provide higher volumetric capacity with each pitch and accurately meter bulk materials.
The live bottom screw feeder consisted of three individual screws with individual drive units. Each drive unit is controlled by a variable frequency drive and can be “fine-tuned” for exact metering.
A cable safety stop control unit provides quick shutoff in an emergency. A cable was externally mounted around all sides of the feeder and connected to the control unit. By pulling the cable, output contacts located inside the control unit are activated and power is shut off. The cable safety stop control unit provides simple, reliable, and long-term operation.
Testimonial
"Storing and metering light density plastic fluff is extremely difficult, but KWS made it looks easy! The engineering services available from KWS add enormous value for Radici and we will be working on many more projects in the future."
Will Rankin, Industrial Engineer – Radici Group
Vertical Hopper Walls Prevent Compression and Bridging of Plastic Fluff
Individual Drive Units with Variable Frequency Drives Provide Accurate Metering
Mass Flow Screw Design Delivers Increased Volumetric Capacity with Each Pitch