Grit Removal System for Turkey Creek WWTP Joplin, MO
Joplin Public Works
Joplin, MO
Allgeier, Martin and Associates, Inc.
Joplin, MO
G & G Construction Co., Inc.
Carthage, MO
Turkey Creek WWTF
Joplin, MO
General Description
The Turkey Creek Wastewater Treatment Plant (WWTP) is located in Joplin, MO and designed for 15 million gallons per day (MGD). The plant was built many years ago but has been regularly updated and repaired. The plant has survived many traumatic weather events, and it has provided reliable service to the community.
Screw conveyors are used in the grit classifier area to remove grit from the tanks. The existing shafted screw conveyors were constructed of carbon steel and severely deteriorated. The shafted screws were also a constant source of maintenance because the internal hanger bearings were submerged in the grit and water. Due to aging equipment and the effects of the harsh environment, the plant required the replacement of two of the three grit removal screw conveyor systems.
The improvements included replacement of the existing grit screw conveyors and related electrical equipment. The new grit screw conveyors were designed to fit the existing tanks with design improvements to improve run time and eliminate maintenance issues.
The new screw conveyors operate in conjunction with the grit classifiers, which are concrete basins fitted with rotary spreaders. Each grit classifier is designed with a channel where an inclined screw conveyor is embedded. Grit falls out of solution by gravity and rotary spreaders convey the grit to inclined screw conveyors.
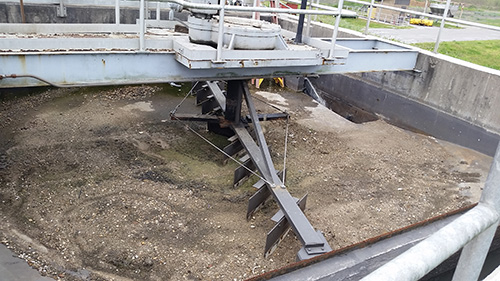
Rotary Spreaders Convey Grit to KWS Inclined Screw Conveyors
The grit is dewatered and lifted by the screw conveyors to dumpsters. The equipment is exposed to the elements and corrosive gases present at the headworks. The new screw conveyors provided by KWS Environmental were designed with abrasion and corrosion resistant materials.
Design Parameters
- Product Type: Grit
- Material Density: 100 Lbs. per Cubic Foot
- Capacity: 40 Cubic Feet per Hour
- Duty: 5 days a week, 8 Hours per Day
KWS Advantages
Grit is Conveyed and Elevated to Dumpsters
The project started with the local KWS Environmental representative working with the consulting engineer and management of the Turkey Creek WWTP to find the proper conveying equipment for the application. The KWS engineering team analyzed the engineer’s design and provided valuable input to the initial design. KWS Environmental provided two new grit removal screw conveyors to fit the existing basins with minimal new control equipment. KWS replaced the existing shafted screw conveyors with shaftless screw conveyors to minimize concerns with corrosion and abrasion. The shaftless design eliminated the need for a submerged bearing.
The concrete channel provided for the new shaftless conveyors was 15-inches wide at the narrowest point, which required special design considerations to allow for removable covers, hold-downs, and liners. The engineers at KWS modeled the concrete channel and new screw conveyors to determine proper fit using 3D Autodesk Inventor allowing the design to be approved with very few comments from the consulting engineer. KWS manufactured the new conveyors to meet a very tight delivery schedule and a KWS engineer visited the site on two separate occasions to verify the installation and start up the equipment. The site visits went very smoothly and the equipment was put into service very quickly.
Special Features
The new KWS Environmental shaftless screw conveyors were designed to handle the abrasive grit and be easier to service. The KWS-350 hardened microalloy shaftless spiral is the hardest and toughest in the industry. The spiral is supported in the trough by AR400 wear bars, which can be replaced en masse or individually. The wear bar strips form a natural channel along the length of the conveyor, which allow grit to be transferred up the incline with ease.
The spirals are kept secure in the troughs using the KWS exclusive hold-down design. To prevent material from freezing inside the conveyor during cold weather, the exterior of the troughs was fitted with heat tracing and insulated with a special glass-foam covered with a stainless steel skin. KWS designed the custom supporting structure to be a bolt-together structure that required no welding or field modification. The submerged conveyor troughs were designed to be grouted in the grit channel.
Testimonial
"We had to no problem removing the first screw conveyor and replacing it. We had to work the concrete to make it fit, but the conveyor fit great. The second screw was hard to remove, but the replacement fit in with no problem."
Dennis Johnson – Project Manager, G & G Construction Co., Inc.
KWS Inclined Shaftless Screw Conveyor Extends to Bottom of Concrete Channel
Special Hold-Down Keeps Spiral in Trough
KWS Inclined Shaftless Screw Conveyor Conveys and Elevates Grit from Classifier
Integral Gearmotor and Simplified Controls Make Operation Simple
Upper End of KWS Inclined Shaftless Screw Conveyor is Insulated with Heat Tracing
KWS Inclined Shaftless Screw Conveyor is Embedded in Concrete Channel