Easy Clean-Out Screw Conveyor for Milled Grain Industry
General Description
Milled-grain food products are used by restaurants, bakeries, and retail markets for the delicious foods that we consume every day. Milling is the process of cleaning, tempering, and grinding cereal grains into flour and other milled grain products. Ground grain was one of civilization’s first foods. Ancient methods of grinding can be traced to the Far East, Egypt, and Rome. As early as 6,700 B.C.
The corn dry milling industry produces a wide variety of yellow and white corn products with the main product categories being degermed corn grits, corn meal, corn flour, and corn bran. These, in turn, are used in a number of common foods, from breakfast cereals, to snack foods, baked goods, beer, and even pet foods.
One of North America’s largest food and ingredient companies operates a plant in Indiana and mills a wide variety of premium corn masa flours used in the production of tortillas and corn chips. The plant can produce nearly 32,000 tons of corn masa flour annually. KWS engineered and manufactured a screw conveyor to transfer corn flour from a cyclone with a rotary airlock and then to a rotary distributor that divides the material into four ports for the sifting process.
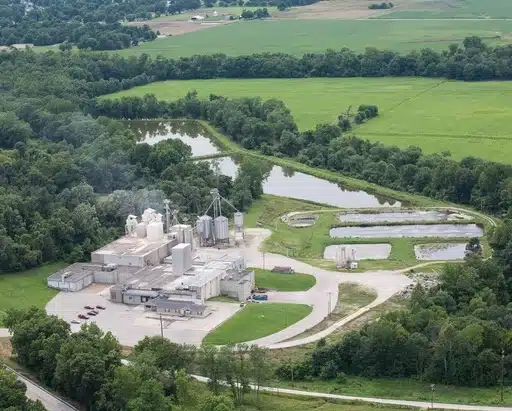
Aerial View of Milling Operation
Design Parameters
- Product Type: Corn Flour
- Material Density: 27 Lbs. per Cubic Foot
- Capacity: 593 Cubic Feet per Hour
- Duty: 24 Hours per Day
KWS Advantages
KWS met with the customer on site to review the specifications and application to develop a long term and
cost-effective solution. KWS coordinated the layout and dimensions, so the screw conveyor fit perfectly within the existing space without compromising the process or functionality.
KWS used the latest modeling software to ensure proper layout of the conveyor within the building as well as mating to upstream and downstream equipment. The new KWS screw conveyor fit perfectly with an allowance for maintenance.
KWS Special Features
The new KWS screw conveyor was installed just below the ceiling with ability for maintenance and wash-down. Drop bottom trough sections provided for easy clean out from the bottom of the unit. Each drop bottom section was hinged on one side and held closed on the other with clamps for easy opening. Interlock safety switches were also installed to help prevent accidents.
Purgeable Cinch Seal shaft seals were used to prevent any leakage of materials from the conveyor. The drive end utilized a unique KWS torque arm trough end which allows the drive unit to float and removes any unnecessary loading on the drive shaft. KWS manufactured a discharge transition to seamlessly match up with the customer’s rotary distributor.
Testimonial
"KWS does very nice work! The new screw conveyor fit into a tight location while providing access for clean out and maintenance. Your engineering team understands how to design for our specific applications. We have more work for KWS in the near future."
Production Engineer – Food and Ingredient Company
Screw Conveyor Transfers Corn Flour from Cyclone to Rotary Distributor
Purgeable Cinch Seals Eliminate Material Leakage
KWS Torque Arm Trough End Allows Drive to Float
Safety Interlock Switches are Located on Each Drop Bottom Trough Section for Safety
Drop Bottom Trough Sections are Opened for Maintenance and Clean Out
Special Transition Matches Rotary Distributor