Dewatered Biosolids Load Out System for Westminster Wastewater Treatment Facility Westminster, CO
City of Westminster, CO
Westminster, CO
HDR Engineering
Denver, CO
Archer Western Construction, LLC
Irving, TX
Big Dry Creek WWTF
Westminster, CO
General Description
Big Dry Creek Wastewater Treatment Facility (BDCWWTF) is part of the Westminster, CO water system and treats approximately 65-percent of the wastewater generated in the City of Westminster. The facility annually treats over 2,580 million gallons of wastewater. Construction, testing, and start-up operations of a new $23 million dewatering facility and other improvements were scheduled to be completed in 2020. Residents experienced a decrease in truck traffic to and from the site due to completion of construction and operation of the new improvements.
BDCWWTF operates 24 hours per day and 365 days per year. Improvements to the plant included an automated biosolids load-out facility. The new system dewaters biosolids via centrifuges that directly feed a KWS Environmental load-out system consisting of a shaftless screw conveyor, two storage bins, rigid and flexible chutes, and multiple slide gates, all designed to load trucks.
During the wastewater treatment process, organic solids, called biosolids, are separated from liquids. These biosolids are treated and transported to Strasburg Natural Resource Farm for soil conditioning. Rich in nitrogen, organic matter, and trace nutrients, these biosolids are an ideal additive for depleted soils.
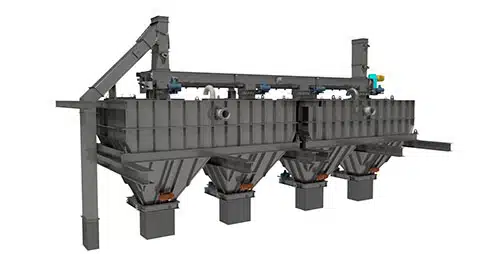
KWS Provided a Complete Biosolids Load Out System
Design Parameters
- Product Type: Dewatered Biosolids (Sludge)
- Material Density: 45 to 65 Lbs. per Cubic Foot
- Capacity: 340 Cubic Feet per Hour
- Duty: 7 Days a Week, 24 Hours per Day
KWS Advantages
KWS Environmental was selected to provide a load-out system that required minimal operator involvement. KWS worked very closely with the consulting engineer, contractor, and local operators to design a system that met the requirements of the process and fit in the available space at the plant. The load-out system design went through several iterations before the final design was approved by the contractor and consulting engineer.
KWS provided valuable input to the design and accommodated changes to the building layout and mating equipment. Structural supports for the new load-out system were analyzed, approved, and stamped by an engineer certified by the state of Colorado. KWS Environmental assisted the contractor during the installation, commissioning, and start-up phases to ensure the system was installed in accordance with the consulting engineer’s design.
KWS Special Features
KWS Screw Conveyor Transfers Biosolids from Centrifuges to Hoppers
The new KWS load-out system included a shaftless screw conveyor, two 1,200 cubic foot storage bins, a two-way gravity diverter, and eight electrically actuated slide gates. KWS also incorporated various chutes, both rigid and flexible, to keep the sludge contained as is loaded into trucks. The conveyor, chutes, and slide gates were manufactured from 304 stainless steel to prevent corrosion while the bins were manufactured from carbon steel painted with a corrosion-resistant paint system. The custom structural supports were designed to bolt together and required no welding or field modification.
The angled sidewalls of the bins, known as hoppers, were lined with bolt-in UHMW sheets to serve as a low-friction surface to aid the flow of sludge toward the discharge openings. The hopper walls were also fitted with electric vibrators to assist in moving any stagnate sludge toward the discharge when the slide gates are open.
Every KWS shaftless screw conveyor comes standard with our exclusive one-piece flanged drive shaft. The drive shaft is machined from solid bar stock and is guaranteed for life. To better protect the equipment and operators, the shaftless screw conveyor was fitted with a speed sensor, emergency pull cord safety stop systems, and fixed covers secured with safety bolts requiring a special tool to remove.
Testimonial
"We have worked with KWS on several projects. We appreciate your commitment to ensuring these projects are a success."
Connor Reger, Project Engineer – Archer Western Construction
Slide Gates Open and Discharge Biosolids to Trucks for Reuse as a Soil Conditioner
Dewatering and Load Out System is Located in Solids Dewatering Building