Conveying Iron Oxide Filter Cake for MP Materials in Mountain Pass, CA
M.W. Watermark
Name and LocationMP Materials
Mountain Pass, CA
General Description
Rare earth elements are vital to our modern technologies and used in electric vehicles, computers, smartphones, and many other products. Most mining of rare earth elements occurs primarily outside the United States causing supply chain issues for many of America’s “green technology” industries. MP Materials operates a mine in Mountain Pass, CA to produce rare earth elements for production of electric cars and wind turbines. Mountain Pass has one of the richest deposits of rare earth elements in the world.
Extensive processing is required to separate rare earth elements from mined ore. As part of the process, MP Materials uses plate-and-frame filter presses to remove water from waste material. KWS provided a twin-screw conveyor to receive dewatered cake material from the filter press, break it up and transport it to trucks for disposal.
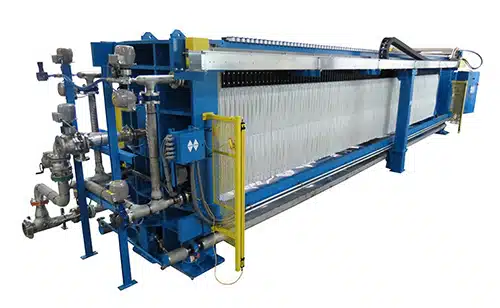
MW Watermark Manufactures Filter Presses to Separate Liquids from Solids
Design Parameters
- Product Type: Iron Oxide Filter Cake
- Material Density: 134 Lbs. per Cubic Foot
- Capacity: 432 Cubic Feet per Hour
- Duty: Continuous
KWS Advantages
KWS excels at solving difficult bulk material handling problems involving corrosive, abrasive, and dense bulk materials. Engineers from M.W. Watermark and KWS worked closely to design a conveying system to receive dewatered iron oxide material and transfer it to trucks for disposal. A flared hopper with breaker bars fit up under the plate-and-frame press to receive and breaking up the material as it discharged from the press. Cake discharged from each plate is two cubic feet in size, weighs approximately 190-pounds, and needs to be broken up prior to entering the twin-screw conveyor. KWS understood the requirements of the application and created a simple, cost-effective solution.
KWS Special Features
Twin Ribbon Screws Convey and Break Up Damp Iron Oxide Filter Cake
KWS designed and manufactured a flared hopper to bolt up to the press, creating a direct connection. The hopper was built with cake breaker bars across the opening, to break up the material discharged from the press.
Directly under the hopper was a KWS twin-screw conveyor to transfer the damp and sluggish filter cake to a take-away conveyor and then truck load-out. The twin-screw conveyor had internal hanger bearings due to the long length. The hanger to supporting brackets had an inverted angle on top to deflect falling material and keep the hangers from being impacted.
Since the bulk material is wet and corrosive, Duplex 2205 stainless steel material was used for construction. Due to the dampness and stickiness of the material, integral leg ribbon screws keep the material from building up on the center pipe. Duplex 2205 material is twice the strength of 304 or 316 Stainless Steel, has superior resistance to corrosion cracking, pitting, erosion, and general corrosion in severe environments and is work hardened.
Testimonial
"KWS equipment is the best in the industry. We have tried other manufacturers, but KWS provides the best engineering support, equipment design and overall manufacturing quality that we expect. There are many more projects in the pipeline and KWS is our partner."
Tim Snow, Business Development Manager – MW Watermark
Each Screw is Driven Independently to Deliver Maximum Torque
Dewatered Filter Cake Discharges to KWS Twin Screw Conveyor and is Transported to Load Out
Flared Hopper is 30-Feet Long to Accommodate Length of Filter Press