Complete Conveying System for Distiller’s Dried Grains at Major Bourbon Whiskey Distillery
Frankfort, KY
Consulting EngineerThermalTech Engineering
General Description
With the oldest continuously operating distillery in America, a major bourbon whiskey producer continues to innovate and develop new processes to sustain its position as one of the leaders in the spirits-making world. They embarked on the design and installation of a new Dryhouse on site to separate Distiller’s Dried Grains with Solubles (DDGS) from spent beer. ThermalTech Engineering was awarded the contract to design, install, and automate this new process.
The initial stages of the new process would include centrifuges, rotary steam tube dryers, mixers, and evaporators for removing moisture and concentrating stillage into DDGS. In the latter stages of the process, mechanical conveyors and storage were needed for dry DDG transfer from the receiving filter to an elevated flat storage room. The dried DDGS is stored in elevated floor hoppers and then transferred from the flat storage room hoppers to an elevated truck loading area.
After an exhaustive evaluation, ThermalTech Engineering chose KWS as a partner to supply the mechanical conveying equipment that would be needed to connect the various pieces of process equipment. This would include shaftless screw conveyors to convey the wet cake DDGS from the centrifuges, shafted screw conveyors to transfer the dried DDG from the rotary steam dryer, screw feeders to meter DDG from the flat storage hoppers, and a bucket elevator to lift the DDG into a Dynatek articulated loading arm for truck loadout. The KWS scope also included various roller slide gates used for maintenance isolation and the selection of different discharge points along the length of the screw conveyors.
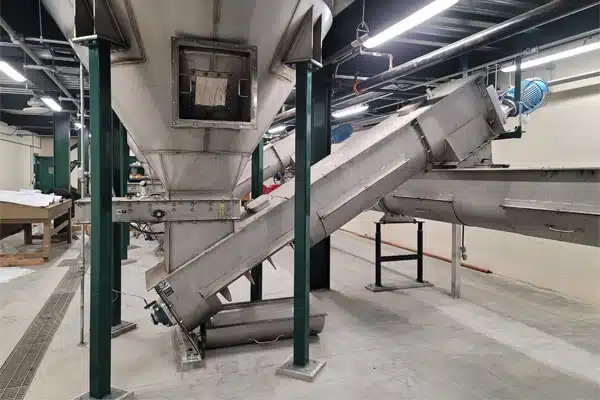
DDGS is Stored in Hoppers and Metered by Screw Feeders
Design Parameters
- Product Type: Distiller’s Dried Grains with Solubles (DDGS) & Distiller’s Dried Grains (DDG)
- Material Density: 30 Lbs. per Cubic Foot
- Capacity: Up to 2,667 Cubic Feet per Hour
- Designed Duty: Intermittent Duty
KWS Advantages
KWS offered multiple mechanical conveying technologies giving ThermalTech Engineering the advantage of sole sourcing this equipment. KWS’s experience with conveying DDGS and DDG at other major beer and spirit producers instilled confidence in the ThermalTech engineers that KWS would be the ideal partner for this ambitious and demanding project. With the new process being installed in an existing building, precision design and engineering were paramount. The KWS engineering team was up for the challenge. The parametric 3D models provided during the design phase were instrumental in the ThermalTech engineers achieving near-flawless system integration and installation.
Screw Conveyors are Used to Transfer DDGS to Mixers and Dryers
KWS Special Features
KWS included pivotal hazard monitoring instrumentation to protect the equipment against catastrophic failure. Shaft-mounted speed sensors detect changes in the rotational speed of the screw conveyors, screw feeders, and bucket elevator. When the sensor detects a change in speed, it alerts the control room of a potential malfunction allowing time to safely shut down the equipment for evaluation. To detect any potential blockages of material flow, capacitance point level plug detection sensors were installed above the screw conveyor and screw feeder discharge spouts. The process may be halted to prevent damage or plugging of other upstream conveying or processing equipment.
At the request of the end user, KWS incorporated bolt-on drop bottom doors along the length of the screw conveyors and screw feeders. These doors provide convenient entry points for the inspection and cleaning of the equipment. To ensure the safety of the plant personnel, the screw conveyors and screw feeders undergo a “lockout/tagout” procedure to confirm that the units are de-energized before the drop bottom doors are removed.
Testimonial
"Given the scope and complexity of the project, the installation of the KWS equipment went great and well exceeded our expectations."
Jeff Reamer, Construction Manager – ThermalTech Engineering
Drop Bottoms Provide Access for Maintenance After All Equipment is De-Energized
KWS Provided Engineering and Supports for Conveyors
Dryers Discharge to Screw Conveyors for Loadout and Storage
DDG is Transferred to Storage Areas and Evenly Discharged for Maximum Usage
Drop Bottoms Provide Access for Maintenance After All Equipment is De-Energized
Bucket Elevators Convey DDG Vertically to DynaTek Loadout Spouts
DDG is Conveyed Vertically to Loadout
DDG Easily Conveys in Screw Conveyors