Biosolids Load Out System for Glenmore WTP Calgary, Canada
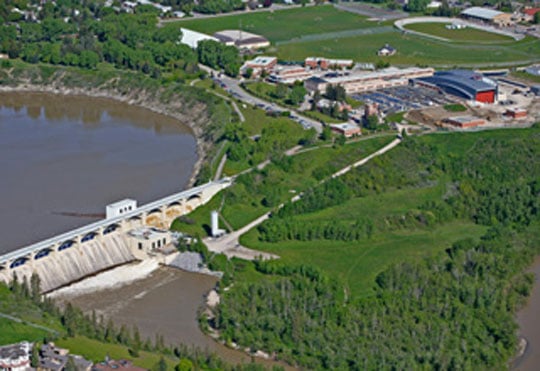
City of Calgary - Water Resources
Calgary, AB
Associated Engineering
Calgary, AB
PCL Construction Management Inc.
Calgary, AB
Glenmore Water Treatment Plant
Calgary, AB
General Description
The Glenmore Water Treatment Plant (WTP) supplies clean water to the southern part of Calgary and region. It was developed as one of the four main components of the massive Glenmore Water Works System, that comprised a storage reservoir and dam, a pumping station, a purification plant (the Water Treatment Plant) and a pipe line system. Originally built in the 1930’s, the Glenmore Water Works System was one of the most significant engineering projects completed in western Canada up to that time and has since been a landmark feature of the city.
The Elbow River flows into the Glenmore Reservoir, which is the source for the Glenmore Water Treatment Plant. Almost all of the water that is removed from the Elbow River for use in Calgary is returned to the Bow River system after treatment in Calgary’s wastewater treatment plants.
A project commissioned in 2011 included improvements to the pre-treatment, filtration and chemical systems, together with upgrading biosolids handling. KWS Environmental was selected to supply the biosolids handling equipment including diverter gates, shafted screw conveyors, pneumatic slide gates and controls.
Design Parameters
- Product Type: Dewatered Biosolids
- Material Density: 55 to 65 Lbs. per Cubic Foot
- Solids Content: 16 to 23-Percent
- Capacity: 1,000 Cubic Feet per Hour (per Centrifuge)
- Duty: 24 Hours per Day, 7 Days per Week
KWS Advantages
The biosolids load out system was fed by two Andritz centrifuges. The system consisted of diverter gates, multiple shafted screw conveyors and slide gates. KWS Environmental designed and engineered the complete system utilizing Inventor 3D modeling so that the new system would fit into the existing building and interface with other process equipment. Installation was accomplished quickly and efficiently which allowed the Contractor to deliver on time and within budget.
The plant layout was designed to be completely redundant. Each centrifuge could discharge biosolids to one of two truck load out stations. The screw conveyors located under the centrifuges were reversible to allow biosolids to be delivered to either truck load out station. The shafted screw conveyors located over the trucks evenly distributed the biosolids by the use of multiple slide gates. The load out system was designed to be reliable and robust so that any required maintenance involved little or no downtime. KWS supported the installation, commissioning and training by providing a qualified and registered engineer familiar with the project, design requirements and equipment delivered.
Special Features
KWS met all the design and operating requirements of the application. All of the KWS Environmental equipment was manufactured from 316 stainless steel for maximum corrosion resistance. The shafted screw conveyors utilized the exclusive KWS Tor-Ri-Flex intermediate bearings. The shafted screw conveyors were designed to span distances of almost 20-feet without the need for an intermediate bearing so only two bearings were required. KWS designed the bearings locations so they were easily accessible and routine lubrication was achieved automatically using spring-actuated lubrication pots.
KWS Environmental diverter gates were used at the centrifuge discharges to separate low solids material from the biosolids cake. Pneumatic slide gates and local control stations at each discharge allowed distributed truck loading in Auto and Local modes.
Testimonial
"This was a large and relatively complex biosolids handling system and we are glad we worked with a partner who understood the requirements and had the experience to deal with any and all issues. Thanks KWS Environmental for providing engineering expertise and high quality equipment."
Virgil Robinson, Project Manager – Andritz Separation