Broke Thickener Repulper Screw for Georgia Pacific Naheola Mill Pennington, AL
GP Naheola Pulp & Paper Mill
Pennington, AL
General Description of the Application
The pulp and paper industry has developed a variety of products that are used by most consumers on a daily basis. Paper products have been produced at the Georgia Pacific Naheola Mill in Pennington, AL since 1959. The principal products manufactured are Quilted Northern & Quilted Northern Ultra bathroom tissue, Brawny paper towels, and paperboard that is manufactured into Dixie food and beverage containers. GP Naheola produces over 650,000 tons of paper, paperboard and pulp annually, or 1,780 tons per day.
Paper broke is a term used to describe the trimmings, waste or otherwise excess product that is produced by a paper machine. Paper broke is gathered up and reintroduced into the paper making process so that nothing is wasted. Part of the recirculation process includes washing the paper broke to ensure it is free of contaminants and then thickening or dewatering it prior to pressing it into paperboard. Screw conveyors are used to convey paper broke back into the paper making process.
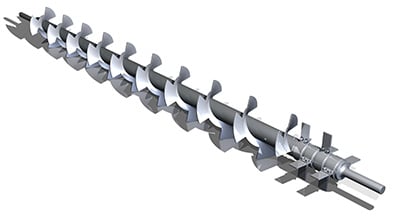
Design Parameters of Application
- Product Type: Paper Broke
- Material Density: Variable – 40 to 60 Lbs. per Cubic Foot
- Duty: 24 Hours per Day, 7 Days per Week
Advantages Provided by KWS
KWS has provided screw conveyors to the pulp and paper industry for over 45 years. With multiple Professional Engineers on staff and decades of experience, KWS is the leader when it comes to providing effective solutions. All manufacturing takes place in Burleson, TX, so our Customers can be confident knowing that their equipment is Made in the USA.
Every Made-to-Order application is verified by performing an engineering analysis to confirm the torque rating of components, mid-span deflection and fatigue loading conditions. Far from being just another screw conveyor manufacturer, KWS is the leading solution provider for the most difficult applications.
Special Features of KWS Design
Tolerances are critical in any industry, but pulp and paper applications typically require the utmost precision possible. Screw conveyors that are used in the paper making process are very special in design. Screws mounted on large diameter pipe are commonly employed to avoid using intermediate hangers for support. Drive and end shafts typically require an interference fit and avoid CEMA standard bolted shaft connections. The CEMA bolted connection uses a slip fit that can leave too much clearance, causing the screw and/or shaft to fatigue and fail prematurely.
Working closely with Motion Industries and the mill, KWS redesigned the Broke Thickener Repulper Screw on large diameter pipe with heavy wall thickness and shrink-fit shafts that were pinned and welded in place. Because paper broke tends to mat and clump together while being conveyed, the KWS replacement screw was designed with cut flights, which agitate the material, breaking up clumps that could cause a plug downstream. KWS added bolt-on breaker paddles that were installed over the discharge of the screw to break up any clumps that make it through the cut flights while also ensuring a full discharge to avoid buildup at the end of the screw housing. The breaker paddles were formed from heavy-gauge steel and are designed to be easily replaced as the bolted connection doesn’t require welding on the screw assembly.