Metering Wood Bark at Georgia-Pacific Mill Crossett, AR
Georgia-Pacific
Crossett, AR
General Description of the Application
Georgia-Pacific in Crossett, AR is a pulp and paper mill which produces tissue, paper and paperboard products for both commercial and residential use. The mill has been in existence since 1902, beginning as a sawmill. In 1955, the mill began producing bleached board, in addition to lumber. Today, the mill supports the GP Bleached Board business for folding cartons, cupstock, platestock, and bleached linerboard applications in addition to tissue.
When preparing logs for the paper making process, logs are debarked. The debarked material is called “hog fuel” which is then stored in large piles and later moved to bins for use as fuel to generate power for the facility. The hog fuel is metered from the bins using live bottom screw feeders with variable-pitch screws. The existing variable pitch screws were failing and being repaired every 2 to 3 months because the screw flights were bending and ripping loose from the center pipe due to the extreme loads on the screws in the flood loaded inlet of the bark bin. Additionally, the center pipe was failing prematurely due to high cyclical bending loads caused by the head load of hog fuel in the bin.
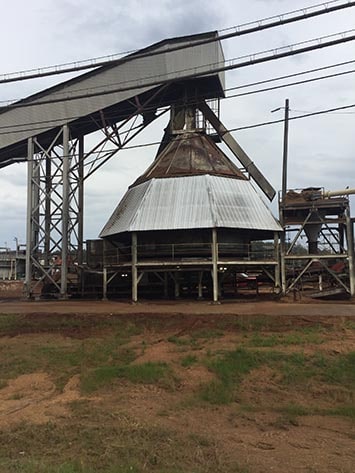
Design Parameters of Application
- Product Type: Wood Bark
- Material Density: 10-20 Lbs. per Cubic Foot
- Conveyor Capacity: 4370 Cubic Feet per Hour
- Moisture Content: 40-60%
- Duty: 24 Hours per Day, 7 Days per Week
Advantages Provided by KWS
A team of engineers from KWS visited the facility and met the Georgia Pacific Woodyard Maintenance Planner to determine the capacity required and the exact needs of the plant. While onsite, the KWS team gathered dimensional information on the existing equipment to determine solutions and recommend bark bin screws which would handle current requirements while giving additional capacity for future growth. KWS tested multiple bulk material samples of the bark to determine accurate bulk densities and flow characteristics. Based on all the information gathered, KWS was able to perform calculations and redesign the screws to accommodate existing requirements, plus allow for future growth.
Special Features of KWS Design
The existing bark bin screw design was not sufficient for the application and did not meet the long-term requirements of Georgia-Pacific. Based on material testing and new calculations, KWS redesigned the bark bin screws with 3/4-inch thick full faced hardsurfaced flights with variable diameter and variable pitch that was continuously welded both sides to larger diameter mechanical tubing with 1-inch wall thickness. The larger diameter center tubing increased the stiffness of the assembly and eliminated the high bending loads on the screws due to the head load. The thicker flights with hardsurfacing were designed to withstand the extreme loading in the bin without failure. KWS also added 3/4-inch thick digger bars around circumference of flights with hardsurfacing on each digger bar to prevent hog fuel bridging in the bin and promote mass flow.
Due to an impending outage, KWS expedited and shipped the screws in 20 working days via hotshot which included submission and return of approval drawings.
Testimonial
"The screw was installed December 19, 2013. We’ve experienced no problems with the KWS bark bin screw. Thanks for the good quality."
Mike Roberts, Woodyard Production Manager – Georgia Pacific