KWS Provides Domestic Source for Replacement Screws
General Description of the Application
Johnson Controls (JCI) is an international company that started with the invention of the electric thermostat in 1885 and has grown to encompass a multitude of industries. One of the foremost concerns for JCI is sustainability, which lead them to build a vehicle battery recycling facility in Florence, SC which opened in 2012. The recycling facility is designed to keep every trace of lead contained while processing an average of 1,600 car and truck batteries per hour. An impressive 99-percent of each battery is recycled and repurposed for future products.
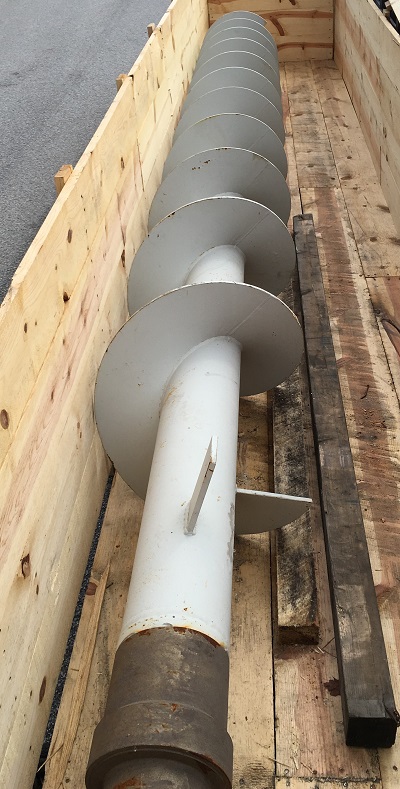
Original OEM Screws Took 6 Months to Deliver
As part of the recycling process, the batteries are broken up and shredded. The lead and plastic materials are separated and conveyed to one of several hoppers with live bottom screw feeders beneath them. The live bottom screw feeders then meter the materials to the recycling process. The original system was designed and provided by a company in Italy. Replacement screws were being ordered from the OEM, but typical lead times were 5 to 6 months including the shipping time. JCI looked to KWS for a solution made in the USA.
Design Parameters of Application
- Product Type: Lead, Plastic
- Material Density: 25-87 Lbs. per Cubic Foot
- Capacity: 60,000 Lbs. per Hour
- Duty: 24 Hours per Day, 7 Days per Week
Advantages Provided by KWS
KWS has many years of experience in the evaluation and design of screw conveyors and screw feeders, so replacing another manufacturer’s screws was no problem.
The existing screws utilized weld-in drive and tail shafts with multiple turndowns and threaded sections. After careful evaluation, engineers from KWS measured every critical dimension and created drawings of the replacement screws for the Customer.
KWS made design improvements to increase the life of the screws, such as shrink-fitting the drive and tail shafts to create a stronger screw assembly. KWS machined the drive shafts from 9-inch OD C-1045 round bar to provide maximum strength for this high-torque application. Each screw is painted a specific color to assist the JCI personnel in identifying exactly what screws they have on hand. With drawings to work from, KWS now provides all replacement screws that can be quickly manufactured, preventing costly downtime waiting for a screw to be shipped from overseas.
Testimonial
"The KWS screws are well made and we can get them in 6 weeks instead of 6 months."
Ben T. – Plant Engineer, Johnson Controls
KWS Replacement Screws Delivered in Less Than 6 Weeks and Fit Perfectly into the Existing System
KWS Measured Original Screws and Created Detailed Drawings