Hard Surfacing
The moving of abrasive materials using standard carbon steel or stainless steel components normally results in rapid wear, frequent maintenance, shortened equipment life, and higher overall operating cost. A common method used to combat the negative effects of handling abrasive materials is hardsurfacing.
Hardsurfacing is the application of a layer of abrasion resistant material over softer standard materials. Hardsurfacing improves component longevity, and lowers overall operating costs.
Features
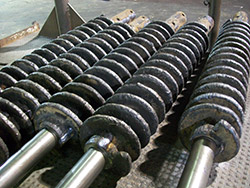
Variety of Construction Materials – Material handling equipment may be constructed out of carbon steel, stainless steel, and special metal alloys.
Variety of Hardsurfacing Materials – Varying combinations of chromium, tungsten, molybdenum, carbon, cobalt, and other more exotic materials are often used in creating hardsurfacing materials. The type of hardsurfacing required can vary depending upon the base metal, the product conveyed, the application, and the environment. The Sales Engineers at KWS will help you select the correct method and type of hardsurfacing materials to fit your specific application.
Variety of Hardsurfacing Methods – Most hardsurfacing is accomplished by conventional welding methods utilizing stick or wire electrodes. Certain light duty and precision applications may require the spray transfer of powdered abrasion resistant substances to the base material using a plasma torch or an oxy-acetylene torch.
Benefits
Wide variety of applications – Hard surfacing can improve component longevity, reduce maintenance events and down time, and lower overall operating costs. KWS Manufacturing Company’s Design and Engineering sales professionals will be able to assist you in meeting the specific requirements, and supplying the right equipment for your abrasive material handling needs.