Automatic Lubrication Systems for Bearings and Drives
Screw conveyors, belt conveyors, drag conveyors, and bucket elevators require periodic lubrication of bearings and key drive components. Some conveyors and bucket elevators use a secondary drive with chain and sprockets to transfer torque. Lubrication of the chain is very important. Periodic lubrication purges contaminants from sensitive rotating elements and reduces friction and heat buildup. Bearing and chain life is extended, reducing costly repairs and downtime.
At most processing plants, lubrication is a manual process whereby the maintenance technician purges the bearing with new grease using a grease gun in a time interval recommended by the bearing manufacturer or OEM. To reduce the need for manual lubrication, KWS offers solutions for automatically lubricating every point on a conveyor or elevator.
The SKF System 24 is a gas-driven lubrication container for a single lubrication point or fitting. It consists of a transparent container filled with suitable grease and a cartridge containing an electrochemical gas cell. Once activated, hydrogen gas is used to actuate a piston to dispense grease at an adjustable interval between 1 and 12 months. The SKF TLMR series utilizes an electromechanical drive instead of a gas-powered piston. The drive is battery powered and the dispense period can be between adjusted between 1 and 24 months.
KWS also designs customized lubrication systems involving multiple lubrication points with a single local reservoir, pump and controls. Consult your KWS sales engineer for the recommended automatic lubrication system for your project.
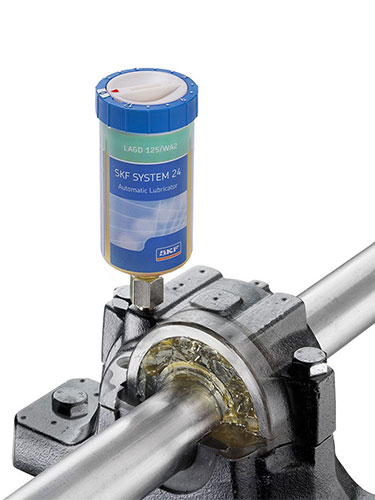
SKF System 24 is Inert Gas Operated for Single Point Lubrication
Features
Multiple Solutions – SKF System 24 is gas actuated with an inert gas and refillable grease container. SKF TLMR is electromechanically actuated and requires replaceable grease cartridges.
Simple Installation and Maintenance – Automatic lubricators simply replace the grease zirk and are filled with grease. Grease is refilled on a periodic basis depending upon frequency of use.
Consistent Lubrication – Automatic lubricators can be located in hard-to-reach areas to provide lubrication at pre-set time intervals.
Benefits
Wide Variety of Applications – The SKF System 24 is suitable for applications for explosion-proof areas and for bearings with low lubrication consumption. The SKF TLMR is suited for applications in non-classified areas and for bearings with high lubricant consumption.
Lower Maintenance Costs – Consistent and automatic lubrication reduces bearing contamination and early failure. Less labor and equipment is required to inspect, repair, and replace bearings.
Improved Safety – Automatic lubrication improves plant safety by reducing maintenance requirements. Operators and maintenance technicians don’t have to climb ladders and get to hard-to-reach lubrication points as often.
SKF System TLMR Can Be Used for Multiple Point Lubrication
SKF MultiPoint Lubricators can Supply Lubrication to 18 Different Points