Ideal Drive Configuration for Live Bottom Screw Feeders
Question
We are currently looking to upgrade the drive package for our 4-screw live bottom feeder. One method uses a single motor/gear reducer driving all four screws through a series of chain drives and the other calls for the use of individual motor/gear reducers on each screw. Is one method recommended over the other?
Answer
Considering the benefits of redundancy, torque requirements and subsequent cost implications, KWS recommends using individual motor/gear reducers for each screw whenever possible.
When considering a single motor/gear reducer with chain drives to the other 3 screws, each screw is completely reliant on the screw it is driven by. If the first screw directly attached to the motor/gear reducer fails, power won’t be transmitted to any other screw in the system. The live bottom feeder and hopper is completely inoperable and will need to be emptied by hand before maintenance personnel can access the broken screw.
With each screw independently driven and you experience a screw failure, the plant will continue to operate at a reduced capacity using the remaining three screws in the live bottom. In addition, the remaining screws are capable of emptying the bulk material from the live bottom feeder and hopper, leaving much less material to be removed by hand to reach the failed screw. By including redundancy in the design, costly unplanned downtime can be minimized.
Similarly, when driving all four screws from a single motor/gear reducer, every screw must be sized to handle full motor torque. As a result, larger shafts, screw center pipe and bearings must be used. For example, if your 4-screw live bottom feeder uses a 20 horsepower motor at 30-rpm motor/gear reducer, full motor torque is approximately 42,000 inch-pounds. To properly design the live bottom feeder to eliminate mechanical failures, the shafts and bearings would be at least 3-7/16-inch in diameter. By comparison, driving each of the four screws with a 5-horsepower at 30-rpm motor/gear reducer, full motor torque is only 10,500 in-pounds. In this case, the minimum shaft and bearing size is 2-7/16-inches in diameter. The required motor/gear reducer is significantly smaller as it is designed to output a quarter of the torque.
While it may seem like adding three motor/gear reducers to the design would increase cost, the opposite is often true. By eliminating chain drives and utilizing smaller diameter shafts, bearings and motor/gear reducers, total equipment cost is typically less than a single motor/gear reducer with chain drives. When adding in the potential saved downtime resulting from redundancy, individual motor/gear reducers offer lower total cost of ownership.
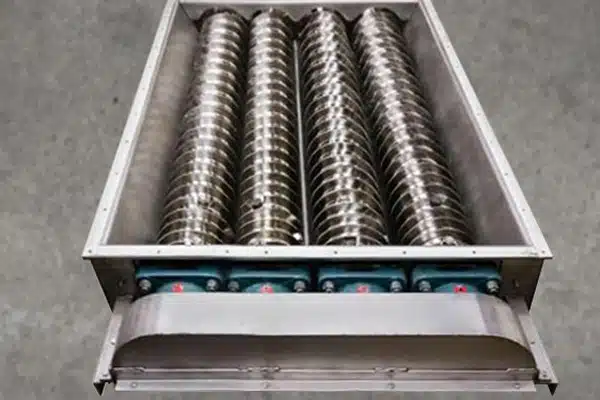
4 Screw Live Bottom Feeder with Single Motor/ Gear Reducer and Chain Drives
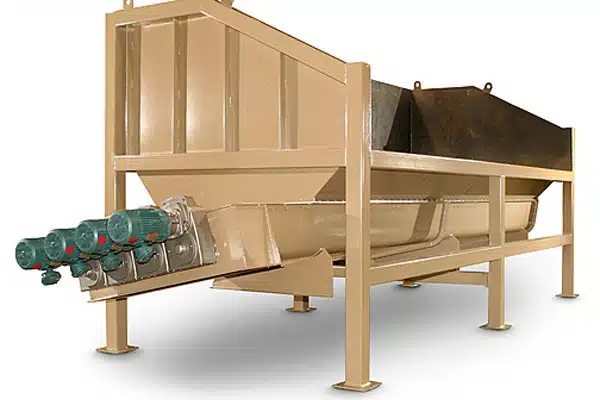
4 Screw Live Bottom Feeder with Individual Motor/Gear Reducers
Driving Each Screw Individually Reduces Size of Shafts, Bearings and Motor/Gear Reducers
Individual Motor/Gear Reducers Provide Redundancy and Minimize Downtime