Twin Screw Feeder with Bridge Breaker for Metering Copper Carbonate Koppers Performance Chemicals in Hubbell, MI
General Description
Koppers Performance Chemicals manufactures wood preservatives and fire retardants for lumber used in residential and commercial construction. Koppers uses copper-based wood treatment technologies which have solid, micronized copper particles suspended in solution and pressure impregnated into the wood. Wood treated with Koppers technology is resistant to decay, termite damage, and fire.
Copper carbonate is a key ingredient to the process but is very difficult to convey. Conveying and processing equipment at the Hubbell plant requires continuous maintenance and replacement, creating downtime and loss of production. KWS has provided long-term solutions to many conveying issues.
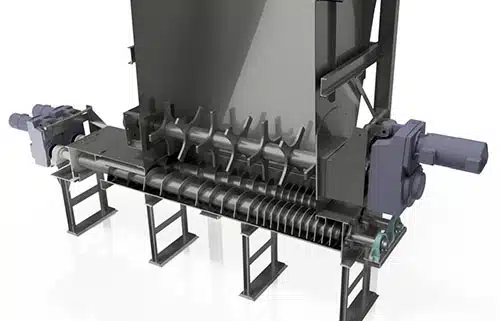
Agitator Breaks Up Lumps and Eliminates Bridging in Hopper
Hopper Stores Dense Copper Carbonate
Design Parameters
- Product Type: Copper Carbonate
- Material Density: 85 Lbs. per Cubic Foot
- Capacity: 308 Cubic Feet per Hour
- Duty: 24 hours per Day, 7 Days per Week
KWS Advantages
Koppers and KWS have been working together over the past several years to solve bulk material handling problems at the plant. KWS is very familiar with conveying and processing difficult bulk materials such as copper carbonate. Working together, engineers from Koppers and KWS have created solutions to improve production and eliminate downtime.
Engineers from KWS have been on site to witness many processes and provide permanent solutions. The specific area of interest was the need to store copper carbonate after discharge from a filter press and then to meter the product into another screw conveyor.
KWS Special Features
KWS designed and manufactured a twin-screw feeder with tall hopper and open side inlet. The open side inlet eliminates concern of connectivity from the infeed conveyor and allows personnel to hand feed the hopper without the need for ladders or lifts. Material bridging was eliminated with the use of bridge breaker located at the bottom of the hopper and equipped with a high torque drive unit. The twin-screw feeder and hopper were constructed from very heavy-duty carbon steel to ensure long life and minimal maintenance.
Each twin screw was designed with oversized center pipe with shrink-fit shafts to handle the high torque generated by the drive units. Split gland seals were used on each end to prevent material leakage. Each screw was driven individually to provide maximum torque and system redundancy. Heavy-duty torque arm trough ends allow the drive units to “float” to reduce stress on the drive shafts. Viewing ports and access doors were mounted in specific locations to assist in inspection and cleanout. Adjustable pipe supports were supplied to mount to the uneven surfaces.
Testimonial
"KWS heavy-duty construction is exactly what we needed to ensure we can operate for years on end without constantly replacing parts. We look forward to having KWS replace all of our equipment before and after this hopper."
Steve Jordan, Engineering and Maintenance Manager – Koppers Performance Chemicals
Each Screw is Driven Independently for Maximum Torque and System Redundancy
Torque Arm Trough Ends Allow Drives to Float Reducing Stress on Shafts