Screw Conveyors for Conveying EAF Dust at Cleveland Cliffs
General Description
Modern steel mills primarily utilize electric arc furnaces to produce molten steel. A by-product of this process is electric arc furnace (EAF) dust, which can be hazardous if released into the open air. To ensure safe operation, air pollution control systems utilizing baghouses are used to recycle air within the plant and remove potentially harmful dust. EAF dust is collected and transported to recycling facilities where zinc and other heavy metals are removed and reused.
Cleveland-Cliffs operates one of the largest steel mills in the world near East Chicago, IN. After years of use, the screw conveyors used to gather and transport EAF dust beneath their baghouses needed replacement. Due to space constraints, the screw conveyors utilized a special housing design that provided access for maintenance. Cleveland-Cliffs had an upcoming scheduled shutdown and needed very quick delivery. With over 50 years of experience and unlimited engineering and manufacturing capabilities, KWS provided a timely solution for the plant’s needs.
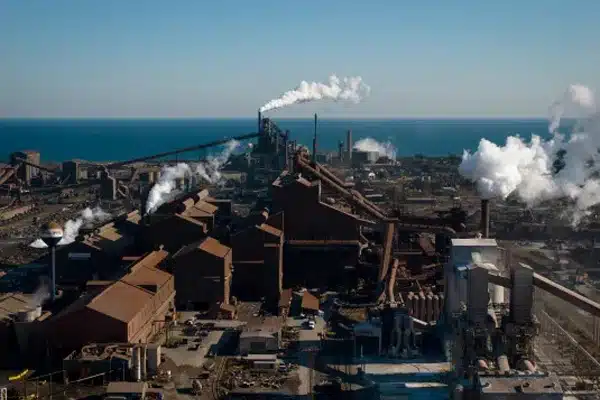
Cleveland Cliffs Operates a Steel Mill in East Chicago, IN
Design Parameters
- Product Type: EAF Dust
- Material Density: 90 to 110 Lbs. per Cubic Foot
- Design Temperature: 200-Degrees F
- Capacity: 200 Cubic Feet per Hour
- Designed Duty: 24 Hours per Day, 7 Days per Week
KWS Advantages
Due to the abrasive nature of EAF dust, hanger bearings must be avoided when possible. KWS designed and manufactured the screws on oversized pipe to minimize deflection. As a result, each screw conveyor only had one screw section, decreasing required maintenance.
The screw conveyors had to fit in a very limited space. KWS technical personnel visited the site and gathered dimensional information, thereby ensuring the conveyors would fit in the space available and match up to the existing baghouse discharges. In addition, KWS personnel were on site during installation to advise best practices and assist with startup procedures.
KWS Special Features
Screw conveyor troughs were offset to allow single-piece screws to be replaced without affecting the bolted connections to the baghouse. Quick disconnect keys were installed on both ends of each screw, providing a means of removing the screw while leaving the shafts and trough end assemblies in place. Without these features, the entire screw conveyor would have to be lowered, and each trough end completely disassembled, in order to replace a screw.
Testimonial
"KWS did an incredible job to make the shutdown. The contractors on both baghouses commented on how well made the KWS screw conveyors were and how straightforward the fit up was. We are looking forward to getting the hopper screws replaced next."
K. Martin, Plant Maintenance Manager – Cleveland-Cliffs
Electric Arc Furnace (EAF) Dust is Extremely Dense and Abrasive
Old Equipment was Replaced with Heavy-Duty KWS Screw Conveyors
KWS Screw Conveyors Gather EAF Dust from Baghouses
Troughs were Offset to Allow Complete Access to Screw Conveyors
KWS Personnel Gathered On-Site Dimensional Information to Achieve Perfect Fit Up
New Screw Conveyors Fit in Very Limited Space