Screw Conveyors to Convey Sawdust Kingsford Charcoal in Summer Shade, KY
Kingsford Manufacturing
Summer Shade, KY
General Description
Kingsford is the leading manufacturer of charcoal in the United States. With seven US plants, Kingsford processes one million tons of wood products into charcoal each year. The charcoal briquet was invented by Henry Ford in 1920 from wood waste created in the production of Model T cars. Henry Ford turned a waste product into a product for beneficial use.
One of the seven Kingsford charcoal plants is located in Summer Shade, KY. The Summer Shade plant was using a 24-inch diameter shaftless screw conveyor to move wood dust between processes. Unfortunately, this conveyor was a source of constant maintenance as the shaftless spiral would routinely fail. When this happened, the conveyor had to be emptied by hand and repaired, a very time consuming process. The spiral would fail at roughly the same location each time due to a combination of misalignment along the length of the conveyor and steam entering the system through the discharge from downstream processes. The steam would prematurely corrode and weaken the spiral, leaving it more susceptible to the fatigue caused by misalignment. After dealing with this issue for many years, Kingsford asked KWS to look at the issue and recommend a solution.
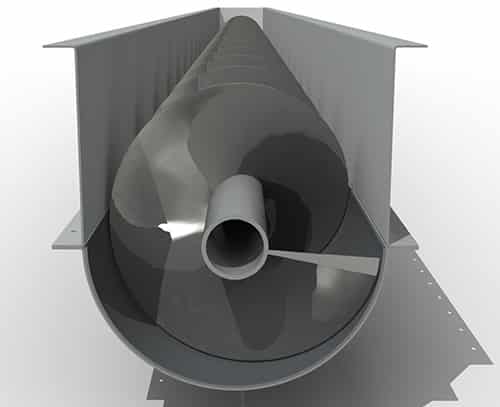
ISO View of Screw Conveyor Showing Inspection Ports
Design Parameters
- Product Type: – Sawdust / Wood Dust
- Material Density – 15 Lbs. per Cubic Foot
- Capacity – 3,500 Cubic Feet per Hour
- Duty – 24 Hours per Day, 7 Days per Week
KWS Advantages
After reviewing the application, KWS recommended using shafted screws that are close coupled and clocked based on successes in similar installations. Shafted screws utilize a center pipe to add rigidity to the design while close coupling the screws creates a continuous helix the full length of the conveyor. The screws ride directly on abrasion resistant AR400 trough liners, eliminating hanger bearings. To make replacing trough liners easy, KWS designed and manufactured channel-style troughs. The bottom portion of the trough is bolted in place, allowing for easy replacement. With more than 45 years of problem solving in the bulk material handling industry, KWS has the necessary experience to tackle any issue.
Special Features
Every aspect of the KWS solution was designed to minimize maintenance costs and increase longevity. The channel troughs and covers were fabricated from 304 stainless steel to prevent corrosion due to the influx of steam in the process. The screws, drive shafts and coupling shafts were oversized for the application and designed for torque ratings well in excess of full motor torque of the drive unit. Inspection ports were included over each of the bolted couplings to allow for easy access and inspection in accordance with preventative maintenance schedules. A KWS bulkhead trough end was used to separate the drive unit from the trough end.
Bulkhead trough ends provide a stand-off space between the trough end and the drive unit. The stand-off space allows fugitive materials to fall out and not contaminate the drive unit. To ensure that no fugitive materials would leak, a KWS split gland seal was installed. KWS split gland seals are completely adjustable with replaceable graphite rope packing that provide a far superior seal when compared to traditional lip seals.
Testimonial
"Everything went right in with no problems. Thanks to KWS we have the right solution in place now."
Steve B., Maintenance Manager – Kingsford Charcoal
ISO View of Screw Conveyor Showing Inspection Ports
Close Up View of Drive End with Bulkhead Trough End