Screw Conveyor for Conveying Peanut Waste at Smuckers Lexington, KY
General Description
J.M. Smucker is a leading consumer goods company with many well-known brands such as Jif, Meow Mix, and Folgers. Lexington, KY is home to the world’s largest production facility where Jif peanut butter is produced. Peanut butter is a nutrient-rich food, containing protein, vitamins, and dietary minerals. The process for making peanut butter starts with planting and harvesting peanuts. After harvesting, peanuts are shelled, dry roasted, cooled, blanched and ground into a homogeneous mixture with other ingredients and flavors to create peanut butter.
Making peanut butter generates large amounts of waste. Peanut waste, typically skins, off-spec meal, fines, and dust, creates challenges for conveying. As part of a process upgrade, a new screw conveyor conveyed peanut waste to a container. The new screw conveyor needed to be easy to clean for sanitary reasons. J.M. Smucker, Dennis Group and KWS created a system to satisfy the demands of the application.
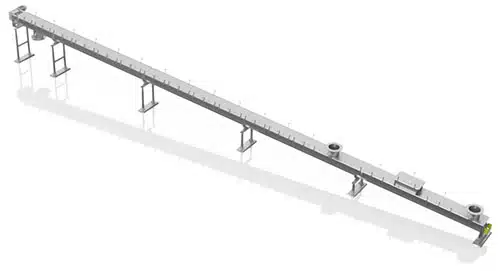
KWS Designed Conveyor for Ease of Maintenance

Product Contact Surfaces Polished to 150-Grit Finish
Design Parameters
- Product Type: Peanut Skins, Meal, Fines, and Dust (Peanut Waste)
- Material Density: 6 to 26 Lbs. per Cubic Foot
- Capacity: 150 to 900 Cubic Feet per Hour
- Duty: 24 hours per Day, 7 Days per Week
KWS Advantages
Dennis Group, J.M. Smucker and KWS have worked together on projects involving peanut waste. Peanut waste can be sluggish, with a high tendency to pack and difficult to convey. Ease of maintenance and special features were desired by J.M. Smucker. Engineers from Dennis Group and KWS visited the Smucker plant to review the application, determine dimensional requirements and understand the needs of J.M. Smucker.
KWS Special Features
KWS designed an inclined conveyor with ease of maintenance while maintaining food grade quality surface finish. Product contact surfaces were polished to 150-grit finish with all welds fully TIG welded and cleaned with no pits or crevices. Every screw conveyor component was water jet cut to ensure clean edges.
Covers were fitted with hinges and heavy-duty backstops for ease of cleaning. Backstops were equipped with magnetic latches to prevent unexpected closing of covers. Conveyor covers were sequenced so only one cover could be opened at a time as a safety precaution. A single interlock switch was provided. A special inlet box with hinged cover was provided for quick inspection and use as a hand dumping port. Inlet and discharge were equipped with a port for personnel to easily check a bulk material sample for quality purposes. Breaker bars were located on the screw at inlet and discharge points to break up large chunks of peanut waste.
Structural supports were supplied as carbon steel with Steel-IT epoxy coating. Bearings and reducer were filled with food grade lubricant.
Testimonial
"KWS quality is amazing, and we designed in all the special features. Both Dennis Group and JM Smucker are happy with the KWS equipment."
Thomas Walker, Project Manager – Dennis Group
Inlet Provided with Sample Port
Hinged Covers Fitted with Backstops for Ease of Cleaning