Food-Grade Dust Collector Screw Conveyor
General Description
Bepex International provides processing equipment and systems for the food, chemical, and mineral industries. They manufacture systems for compacting, drying, mixing, and reducing the size of bulk materials. For this project, Bepex required a sanitary screw conveyor to mount to the bottom of a dust collector. Given our joint success with past projects, KWS was the only choice to engineer and build the ideal solution.
Fugitive dust is prohibited in most modern industrial plants. Dust creates environmental, operational, and public hazards; therefore, dust collectors are used to collect dust safely and efficiently. They work very much the same as a household vacuum cleaner, but on a larger scale, utilizing a large blower to create a vacuum into a baghouse with a collection hopper. The dusty air is collected at various points in the manufacturing process and pulled through bags that filter out the dust.
The clean air is then exhausted from the system. Most of the dust falls off the bags and settles at the bottom of the hopper where a screw conveyor is used to transfer it away. The purpose of the KWS screw conveyor was to convey the accumulated dust to a single point for discharge through a rotary airlock. The dust was then recirculated back into the process so that it is not wasted.
Design Parameters
- Product Type: Calcium Butyrate Salts
- Material Density: 48 Lbs. per Cubic Foot
- Capacity: 124 Cubic Feet per Hour
- Design Pressure: +/- 2 psig
- Design Temperature: 160 degrees F
- Duty: 24 Hours per Day
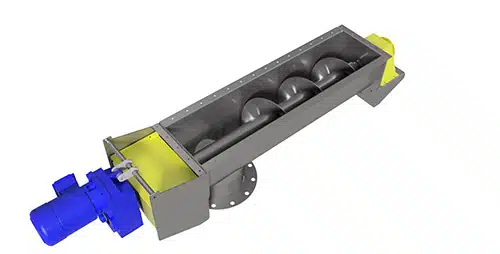
KWS Screw Conveyor Bolts to Dust Collector
KWS Advantages
Bepex and KWS have formed a relationship because both companies manufacture high-quality equipment. Engineers from KWS evaluate and make design recommendations for applications provided by Bepex. KWS has developed specialized design standards for screw conveyors used in dust collector applications. System flow rate is typically limited by airlock capacity. If used intermittently, a screw conveyor must be designed to prevent overfeeding the airlock and causing an upset condition.
KWS design standards also focus on the source of pressure and/or vacuum and the placement of the rotary airlock. In this application, the baghouse has a long rectangular hopper with a screw conveyor bolted to the baghouse hopper bottom with an airlock bolted to the screw conveyor discharge. The screw conveyor was designed to hold both positive and negative pressures. KWS verified the pressure rating of the conveyor by performing a hydrostatic pressure test prior to shipment.
KWS Special Features
Since the dust was to be recirculated back into the process, KWS manufactured the screw conveyor using 304 stainless steel with a polished finish free of pits and crevices. This includes using studs to attach the shaft seals to the trough ends and shrink fit shafts to eliminate all internal bolted connections. All internal surfaces and welds were cleaned, ground flush, and polished to a 150-grit finish bolstering the sanitary design requirements.
For sanitary applications, KWS has developed a unique torque arm drive arrangement. The screw is supported on each end by pillow block roller bearings. The KWS torque arm trough end supports the shaft-mounted gear reducer and allows it to “float” on the drive shaft, eliminating any binding and potential fatigue failure.
Bepex requested the use of purged, packing-type shaft seals. KWS purgeable flanged gland seals consist of an outer housing, multiple rings of packing, a follower, a bronze lantern ring, a regulator, and a gauge. For this application, KWS used FDA compliant (21 CFR 177.1550) ½-inch square mineral oil-lubricated PTFE braided rope packing material that ¬fits tightly in the outer housing and around the shaft diameter. The follower is used to compress the packing and create a seal between the shaft and housing. The nitrogen purge creates a positive pressure in the seals to overcome the internal pressure in the conveyor.
Testimonial
"KWS was a delight to work with on this project and delivered a beautiful piece of equipment. I’m looking forward to working with KWS on future projects.”"
Lisa Nixon, Project Manager – Bepex International
Torque Arm Trough End Allows Drive Unit to Float
Purgeable Flanged Gland Seals Keep Dust Contained