Design-Build System for Prototype Gasification Process
General Description
Bioenergy is renewable energy derived from biological sources, including food, plastic, and wood waste. Bioenergy solutions are in increasing demand as a source of energy and much more environmentally friendly when compared to traditional energy sources such as coal and natural gas. A U.S. based energy development company was interested in a material handling system for a revolutionary gasification process they developed. Gasification is a process that converts organic materials into gaseous fuels by reacting the material at high temperatures without combustion and with a controlled amount of oxygen. Since the project required heavy duty, highly engineered bulk material handling solutions, KWS was the best choice. KWS designed and manufactured a complete mechanical system for the gasification process. This prototype project required designing the system from initial concept and manufacturing each piece of equipment in the process.
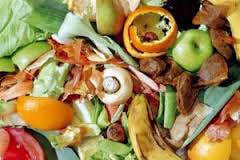
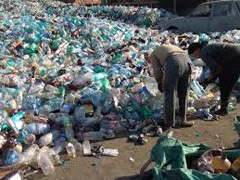
Design Parameters
- Product Type: Damp, Sluggish Waste
- Material Density: 25 Lbs. per Cubic Foot
- Capacity: 50 Cubic Feet per Hour
- Duty: 24 Hours per Day, 7 Days per Week
KWS Advantages
The Customer contacted KWS after reviewing the multitude of special applications and equipment offerings on our website. After many discussions it was determined that KWS was the perfect partner to help develop their new process. KWS worked to totally understand the project parameters such as capacity, heat transfer, space constraints, maintenance and safety. The Customer travelled to Texas and meet the KWS team in person during the design stage and develop the solution together. The KWS engineering team created a system layout in AutoDesk 3D Inventor and provided a detailed proposal. The system layout was easily modified to meet the changing requirements of the project. KWS then provided each piece of equipment in the process making procurement and installation very easy. Working together, a fully engineered system including hoppers, conveyors, and supports was developed.
Special Features
KWS designed and manufactured every piece of mechanical equipment on the project from the initial feed hopper to the final classifier screw conveyor. The initial feed hopper was designed to hold six hours of waste to feed the downstream process. KWS engineers designed the hopper with special geometry and structural supports to fit in the tight layout. A special tubular screw feeder metered material from the hopper to a rotary airlock. KWS designed a special lower end bearing on the screw feeder to eliminate material leakage. The screw feeder fed a rotary airlock which then fed the KWS pressure vessel. The pressure vessel utilized a ribbon screw and jacket housing. The ribbon screw rotated very slowly to allow retention time for the gasification process. KWS designed special shaft seals to hold pressure in the vessel while under elevated temperature. The jacket on the pressure vessel provided the necessary heat transfer for the gasification process to convert the organic material into gas which was extracted from the vessel. The remaining solid material was converted to ash. The ash discharged to a classifier screw conveyor. The classifier screw conveyor had a water-filled hopper to quench the hot ash. The classifier screw then dewatered and conveyed wet ash up an incline to containers. The pressure vessel and classifier were constructed from 316 stainless steel due to the requirements of the process.